Review of welding problems and allied processes and their solving using metal magnetic memory effect
Dr. A. Dubov, S. Kolokolnikov
The welding exists in the world more than 100 years, however the many problems of a quality control of products welded joints and reliability control of welded constructions, till now take place. Among the most important problems are:
- Low effectiveness of traditional means and methods at stress-strained state control of welded joints and determination of stress concentration zones - the sources of damages development.
- Lack in the general practice of norms on defect size tolerances from the position of fracture mechanics.
- Structure buckling or its shape and dimensions variation due to inhomogeneous heating and cooling at welding.
- Lack of effective non-destructive (NDT) methods of quality control of thermal and other welded joints treatment technologies for residual stresses relief.
- Lack of effective methods of contact welding NDT in products of mechanical engineering; till date in practice detachment testing is conducted by impact at the spot welding location with hammer and chisel.
- Selection of optimum welding technologies, deposits, spraying, is a problem task.
- Low effectiveness of traditional NDT methods at control of contact welding of pipes, fillet and welded T-joints.
One of the important and complex problems of a modern non-destructive testing (NDT) of quality of different types weld joints is the searching and definition in them of "a weak link" in a uniform overall system of the factors "structural-mechanical heterogeneity - flaws of a weld - constructive and technological stress concentrator", i.e. zones with high heterogeneity of the stress-strained state or zones of stress concentration (SCZ). It is important for optimisation of technological procedure both at manufacture of welded joints, i.e. immediately after welding, and at their exploitation.
Traditional non-destructive testing, oriented only at detection of discontinuity flaws in welded joints, cannot provide authentic assessment of their quality. It is difficult for a welding technologist to reveal the reasons of weld unsoundness and improve welding technology based only on NDT results.
In conditions when many factors influence reliability of welded joints, it is necessary NDT method for integral estimate of welded joint metal state.
Now in Russia a principally new method for diagnostics of products metal and welded joints with usage of metal magnetic memory (MMM) is developed at a level of the national standard and successfully applied in various industries.
The MMM method is oriented to solution of the above indicated problems of base metal and welded joints NDT on industrial and transport objects.
Method of metal magnetic memory is non-destructive testing method based on the analysis of distribution of self-magnetic leakage field (SMLF) on components’ surfaces for determination of stress concentration zones (SCZ), imperfections and heterogeneity of metal structures and welded joints.
By reading SMLF, reflected residual magnetization, which is formed during welding, the unique opportunity is given us to execute an estimation of an actual state of a weld. And this estimation is integral and represents in each weld simultaneously features of a structural state, distribution of residual stresses and defects of welding.
The forming of magnetic (domain) structure in welded joints occurs simultaneously with crystallization at metal cooling in the magnetic field of the Earth while transiting through a Curie point (768°С) under action of stresses and strains arisen from welding. On arising imperfections of welding the points of domains attachment are formed with an exit on a surface of a weld as self-magnetic leakage fields. Thus, by reading SMLF, which are formed during welding, the opportunity is given us to execute an integral estimation of an actual state of a weld.
The inspection is carrying out by MMM method without dressing of metal and special magnetization. MMM method allows to carry out express quality control of welded joints in a manual both automatic mode at mass production of various products from carbonaceous, austenitic and ferrite-austenitic steel grade.
The inspection is carrying out with usage of the specialized small-sized devices with self-contained power supply, scanning and recording devices. The magnetometric testers of stress concentration (TSC) have no analogues. The devices are manufactured by Energodiagnostika Co. Ltd (Moscow, Russia), are certificated in Gosstandart of the Russian Federation and included in the state register of measuring instruments.
The inspection scheme of butt welded joint is shown on the figure 1. As it is visible from the figure 1, at inspection the ferro-probe converters 1 and 3 is arranged in heat-affected zones (HAZ) from both sides of a weld, the converter 2 is arranged between them in the middle, and the converter 4 is arranged vertically in the opposite direction and intended for tuning out of an external magnetic field.

Fig.2, а shows typical distribution of residual stresses on a welded joint of plates. Fig.2, b shows distribution of the tangential component of the magnetic leakage field Нрx registered at MMM inspection at measurement of the field perpendicular to the weld. These figures show a good qualitative convergence of residual stresses and the magnetic field distributions.
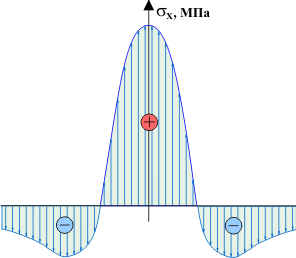
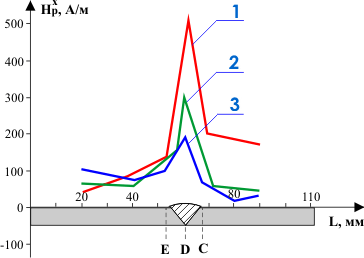
It is known that the on-line inspection of welded joints heat treatment quality is conducted, as a rule, only by measuring of metal hardness. However, such spot inspection does not ensure the absence of mechanical stresses concentrators across the entire weld and in the regions adjacent to it.
Let us further consider the MMM method effectiveness at quality control of the weld heat treatment on a ⌀220х20 mm pipe length of the 12Cr1MoV type low-alloyed steel grade. Heat treatment was conducted with weld metal heating from the induction coil up to 700°С with subsequent cooling in air.
Fig.3 presents magnetograms characterizing the pipe length's stress-strained state far from the weld (3, а) and the weld metal respectively before (3, b) and after the heat treatment (3, c). The magnetograms were obtained as a result of MLPC measurements along the pipe and the weld perimeter according the scheme presented in Fig.1. From comparison of Fig.3, b and 3, c it is seen that the magnetogram registered on the weld after the heat treatment turned out to be similar to that registered in the initial state on the pipe surface far from the weld. The experiment shown in Fig.3 suggests a conclusion that a magnetogram measured along the pipe perimeter near the welded joint, where there is no influence of welding, can be taken as a standard reference sample.
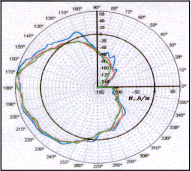
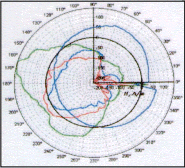
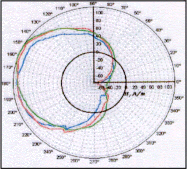
Fig.3. Magnetograms characterizing the pipe length's stress-strained state far from the weld (a) and the weld metal respectively before heat treatment (b) and after heat treatment (c).
Fig.4 shows measurement results of the Нр field normal component characterizing distribution of residual stresses and strains after welding of two identical plates. During welding plates were loose and bent slightly upwards. The Нр field distribution in the considered case shows visually the influence of plates geometrical dimensions and their buckling on residual strains and stresses distribution level and pattern.
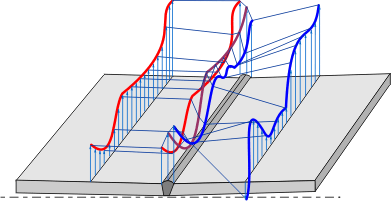
Fig.5, a shows the Нр field distribution on the pipe welded joint registered in heat affected zones (HAZ), and Fig.5, b shows distribution of residual stresses measured on the weld by an X-ray diffractometer in the same zones.
The welded joint quality according to the MMM method is assessed by the distribution pattern of the magnetic field Нр and its gradient dНр/dx where dx is the minimum distance between two adjacent measurement points of the Нр field. The gradient value is determined automatically as a modular difference |ΔНр| divided by the discrete distance Δх between the two adjacent measurement points, set at preliminary adjustment of the instrument.
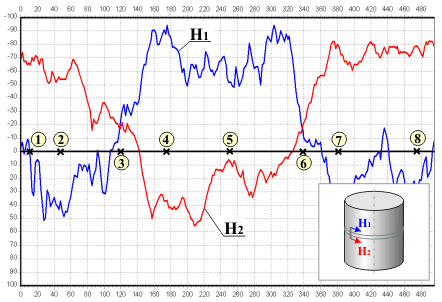
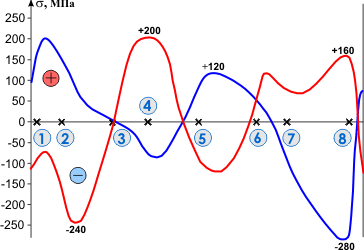
1...8 - points of stress measurement by an X-ray diffractometer symmetrically from two sides of the weld in HAZ;
--- results of stress measurement corresponding to Н1;
--- results of stress measurement corresponding to Н2.
In the Fig.6, a the distribution of the normal component of a field Нр lengthways of the inspected weld segment of the lower floor of the polymerization reactor at the enterprise "Anwil" S.A. (Vlotslavek, Poland) is shown. In the Fig.6, b the disposition of detected cracks is marked. In zones of the detected cracks the polar distribution of a magnetic field on channels Н1 and Н2 is recorded. The segment of a SC line (Нр=0) (see Fig.6, b) with the maximal gradient dНр/dx is situated in HAZ of the weld and is the prolongation of the detected crack.
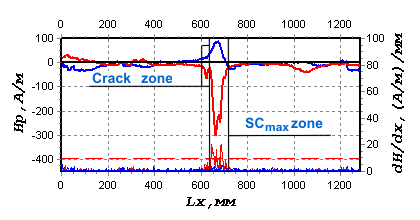
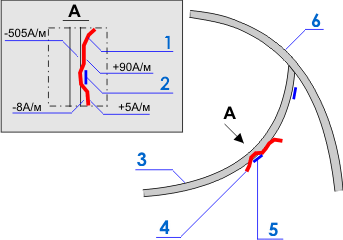
As a result of inspection the following outputs and recommendations were made:
- The crack is an developing imperfection in the direction of the maximal SCZ.
- Removing of metal and welding should be carried out not only in area of detected crack, but also in area of maximal stress concentration for prevention of a crack development while in service.
It is known that the residual strain of the weld metal is formed due to shear plastic strain occurring at crystallization in the course of metal cooling. Diagnostic parameters Нр and its gradien Кin (dНр/dx) owing to "magnetic-dislocation" hysteresis due to duality of the magnetic plane and the glade plane of dislocations, reflect distribution of residual strains and stresses along the welded joint perimeter.
The ratio between limiting values of magnetic parameters mlim , Кint, Кinyand mechanical characteristics of metal σt and σy is given in the paper [1]:
mlim = Кint / Кiny ≈ (σt / σy)2, (1)
where mlim - is magnetic index of limiting strain hardening; Кint and Кiny - are gradients of a field obtained at tensile test of samples at attainment of the yield strength σy and the tensile strength σt accordingly.
It should be noted that the ratio (1), obtained in the course of experimental investigations, was confirmed by the design investigations presented in the paper [2], and it is conditioned by the squared relationship of the parameter Кin to the magnetic and, accordingly, the mechanical energy accumulated in the metal of a SCZ.
The method of the field gradient Кint and Кiny determination in industrial conditions is stated in paper [1]. As a rule, the maximum value Кinmax revealed in certain HAZ, corresponds to Кint and the average value Кinave calculated for all HAZs revealed at equipment inspection, is conventionally equated to the value of Кiny.
Then the ratio (1) can be expressed as follows:
mlim = Кinmax / Кinave ≈ (σmax / σave)2, (2)
where σmax and σave - are accordingly maximal value of stress in SCZ and average value of stress for all SCZs detected at the inspection.
Ratios (1) and (2) were obtained in the course of laboratory and industrial investigations for the base metal. These ratios can be applied to welded joints, except for local stress concentration zones due to welding defects (pores, slag inclusions, poor penetration, etc.).
According to [3], the stress concentration coefficient for a welded joint is equal to:
Кd ≈ σmax / σave , (3)
where σmax - are maximum stresses in HAZ; σave - is an average stress in a welded joint.
Paper [3] gives evaluation of Кd :
- 2÷3 for pores;
- 3÷10 for slag inclusions;
- 10÷100 for cracks, undercuts and poor penetration in the weld root.
It is obvious that ratios (1) and (2) can be also used for local HAZs due to welding defects with correction for defect dimensions and depth of their bedding.
Here it is important to point out the delusiveness in the existing approaches of various inspection means developers at assessment of residual stress distribution in welded joints. As a rule, according to the results of the inspection by various methods (strain measurement and interferometry with metal drilling, X-ray, UT, Barkhausen effect, the magnetic anisotropy method, etc.), the level of residual stresses on welds does not exceed the yield strength σy, which, as a rule, does not correspond to the actual distribution of stresses.
As the practice shows, the level of the directed residual stresses (normal or tangential) in a SCZ may meet 1000 MPa and greater. This stress level may have much greater values in the zones of the developing welding defects and cracks. These practical observations clearly confirm the results of welded joints inspection by the MMM method in a SCZ and outside it combination, for example, with hardness measurement and conversion of its results to stress units. For example, the level of "contact" stresses measured with hardness gages at MEI in SCZs, detected by eth MMM method, often met 1500 MPa and greater. One should keep in mind that strains and stresses are volumetric and have at least three components (radial and two tangential) in each inspection point.
Distribution of SMLF in each inspection "point", measured with three-component sensors with the accuracy up to 1 mm on the weld metal surface and in HAZ, according to the available technique, directly reflects the triaxial distribution of residual stresses and strains. At that it isn't important to know the level of absolute stresses (though this problem is solved in the MMM method!), but their distribution to the depth and along the surface. And the most important thing is, at the same time, not to allow the limiting state of the metal before the crack formation.
Now in Russia the method of metal magnetic memory has obtained wide development:
- More than 45 guiding documents and techniques for inspection of equipment in different industries are developed.
- Three standards of Russia are approved: GOST R ISO 24497-1-2009 "Non-destructive testing. Metal magnetic memory method. Part 1. Terms and definitions", GOST R ISO 24497-2-2009 "Non-destructive testing. Metal magnetic memory method. Part 2. General requirements", GOST R ISO 24497-3-2009 "Non-destructive testing. Metal magnetic memory method. Part 3. Inspection of welded joints".
The International Standard ISO 24497-1, 24497-2, 24497-3 on the metal magnetic memory method is approved in 2007 as a result of positive voting among 18 IIW member countries and more than 10 ISO Committee countries.
References
1. Dubov A.A., Dubov Al.A., Kolokolnikov S.M. Method of metal magnetic memory and inspection devices. Training handbook. Moscow: ZAO "TISSO", 2008. 365p.
2. Vlasov V.T., Dubov A.A. Basis physics of the metal magnetic memory method. Moscow: ZAO "TISSO", 2004. 424p.
3. Fedorov S.A. Quality control of welded and soldered joints. Training handbook. Moscow: MATI, 1989. 201p.