Quality control of cast valves using the metal magnetic memory
Dr. A.A. Dubov
It is commonly known that metallurgical defects create high level of residual stresses (RS) in local zones of the cast iron and steel valve bodies. As a rule, RS monitoring at valve manufacturing plants is not performed. Detection of casting defects in deep layers of body metal using ultrasonic testing is challenging. Due to complex configuration of casting defects inside the body metal, there are currently no clear instructions for defects detection using ultrasonic testing (UT).
Every time ultrasonic testing has to be performed individually on each valve unit in the search mode (selection of beam frequency and tilt angle, selection of inspection area on the body surface).
At present, main gas pipeline shutoff and control valves' technical condition is assessed in accordance with STO Gazprom 2-4.1-406-2009, and of production tree valves – in accordance with OJSC Orgenergogaz technique. In both documents, the metal magnetic memory (MMM) method is included for its application as an express method for detection on valve body surfaces of stress concentration zones forming due to casting defects in combination with workloads.
It is well known that application of the MMM method does not require any surface preparation. Inspection can be performed both on deactivated valves and when they are operated under load, through a layer of paint and along with this natural magnetization of the metal is used. Basic methodical guidelines for the MMM method application are provided in the Training Handbook [1].
When including the MMM method in these guidance documents, it was assumed that the MMM method should be a priority in relation to all other non-destructive testing methods (UT, thickness measurement, hardness measurement, etc.), which are recommended for valves' condition assessment. However, due to the fact that guidance documents do not contain clear instructions on the application procedure of all the listed NDT methods, their purpose and complementarity, in practice each NDT method is applied independently, without any relation to each other.
Figure 1 shows an example of a ball valve body inspection of CS-1 ⌀400 Gas Compressor Unit-1 of LLC Gazprom transgaz Saratov Ekaterinovsky line operation section main gas pipeline.
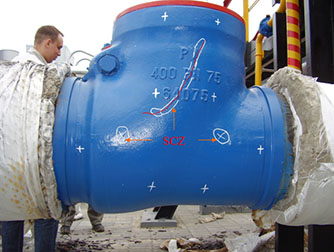
Cross-shaped (+) chalk marks indicate the zones of the body metal thickness and hardness inspection on the external surface, recommended by the instruction for these NDT methods. Based on the results of the wall thickness and hardness measurements in the indicated inspection zones, no deviations of these parameters compared to the design ones were identified. Here, in Figure 1, the zones of magnetic anomalies detected by the MMM method are shown. These anomalies correspond to stress concentration zones (SCZs), the occurrence of which, as a rule, is caused by casting defects and workloads.
In one of the zones detected by the MMM method, after the metal dressing, an extended ~ 250 mm long and at least 5 mm deep crack was detected on this body (based on the eddy current inspection data). This example clearly illustrates the methodological shortcoming of guidance documents in part of recommendations on application of various NDT methods. It was necessary to measure thickness and hardness, first of all, in the SCZs detected by the MMM method. Our experience demonstrates that, as in this case, hardness and thickness values in SCZs significantly differ from the design ones, especially if these zones already contain a developing damage.
One should also note here that it is recommended to perform ultrasonic testing in all SCZs detected by the MMM method in order to identify presence of defects, their length and depth. Application of the eddy current test method and the appropriate instruments that do not require valves' surface dressing is recommended to identify the presence of surface cracks.
It is known that identification in practice of cast products defect presence and size using the ultrasonic method is a difficult task. Combined with the MMM method, the task of valve body casting defects monitoring is greatly facilitated. MMM-inspection results provide the possibility to indicate the UT piezo transducers installation location and the beam inlet angle with an accuracy of 1 mm.
Let us consider another example from the practice of inspection by the MMM method of a ⌀700 mm ball valve, performed by Energodiagnostika Co. Ltd. expert at Gazprom transgaz Saratov LLC Bashmakovsky line operation section main gas pipeline.
Figure 2 shows the magnetogram of the magnetic field gradient distribution recorded during the inspection along the perimeter of the exit (downstream with the gas flow) valve end.
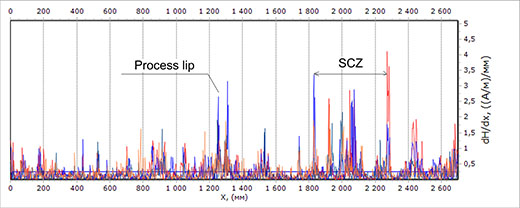
Figure 3 shows a fragment of this valve exit end with detected cracks after metal surface dressing in the SCZ.
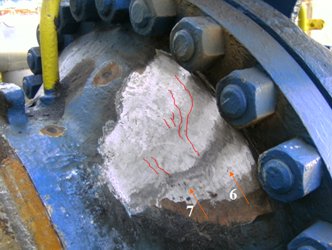
Figure 4 shows a fragment of this zone after sampling of the cracked metal. It can be seen that the specimens metal depth and area are quite significant.
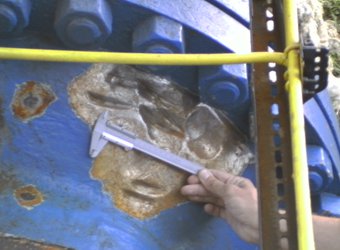
The inspection experience of similar design ⌀700 mm ball valves shows that SCZs detected by the MMM method, and, accordingly, developing cracks in these zones caused by casting defects, are mainly located on the exit thickened valve end.
It should be noted here that not in all SCZs detected by the MMM method, the detected defect sizes and the danger of their development to through ones are the same. The main task of the MMM method is to perform, based on the inspection results, classification of SCZs and detected defects by the degree of their hazard. To do this, quantitative criteria should be developed for similar valve designs based on practical inspection data. For example, inspection by the MMM control of 18 identical ⌀700 mm ball valves at three compressor stations of Gazprom transgaz Saratov LLC resulted in detection of 101 SCZs. Of these, only approximately 15 SCZs have developing casting defects. Moreover, in combination with the ultrasonic method, of these 15 SCZs, it is possible to name 3-4 SCZs, which are the most dangerous for the cracks development on specific valve numbers for their periodic inspection. But in order to make such a decision, a special comprehensive inspection technique and an appropriate OJSC Gazprom guidance document should be developed.
Similar problems were identified during the inspection of production tree valve body parts. It is known that gas pressure inside production tree valves reaches 200 kGs/cm2, and wall thicknesses on this type of valves is much larger compared to shut-off and control valves at the compressor station. With larger wall thickness, casting defects on production tree valves were detected at a depth of 20÷30 mm and more during the comprehensive inspection using the MMM and the UT methods.
Based on the considerable experience in inspecting production tree valves, obtained as a result of a large amount of work performed by Energodiagnostika Co. Ltd. experts jointly with OJSC Orgenergogaz experts at Yamburggazdobycha LLC enterprises, a “Technique for detection of stress concentration zones in production tree valve body parts using the MMM method” was developed as far back as in 2000. However, during the development of OJSC Gazprom guidance document, the main provisions set out in Energodiagnostika Co. Ltd. technique were not taken into account. This technique specifies quantitative criteria for assessment of the metal limiting state in SCZs. The guidance document only recommends application of the MMM method along with other NDT methods.
In conclusion, the following should be noted. Analysis of cast valve body damages shows that the main reason is presence of casting defects. Due to the complex configuration of casting defects in the body metal volume at valve manufacturing plants, there is a problem of these defects detection by non-destructive methods. This article presents the experience of comprehensive inspection (by the MMM method in combination with UT) of bodies of cast valves installed on high pressure gas pipelines. Under conditions when the MMM method preliminarily identifies in the express control mode presence or absence of casting defects with indication defect locations on the external body surface, the efficiency of detecting discontinuity flaws in the metal volume by the ultrasonic method is significantly increased. In many cases, when a SCZ, detected by the MMM method on the body surface, is known, it is possible to detect casting induced discontinuity flaws inside the metal using an ultrasonic thickness gauge.
Performance of such comprehensive inspection of casting defects in valve bodies is recommended both at manufacturing plants and in the conditions of their operation.
When developing practical techniques of the proposed cast valve bodies comprehensive NDT, it is necessary to take into account the degree of the detected casting defects hazard. As the experience of valves MMM-inspection shows, some casting defects may create high concentration of stresses and, consequently, cause cracking up to formation of through cracks, and other defects are “still” and do not create stress concentration. The main purpose of the MMM method is precisely to assess the level of stress concentration in detected SCZs using quantitative magnetomechanical parameters.
Reference
1. A.A. Dubov, Al.A. Dubov, S.M. Kolokolnikov. Metal magnetic memory method and inspection instruments: Training Handbook. Moscow: Publishing House "Spektr", 2012. 395 p.