Non-contact magnetometric diagnostics of pipelines and perspectives of its development
Dr. A. Dubov, Dr. Al. Dubov
Non-contact magnetometric diagnostics (NCMD) is based on measurement of distortions of the magnetic field of the earth (Нearth), conditioned by the variation of the pipe metal's magnetic permeability in stress concentration zones (SCZs) and in zones of developing corrosion-fatigue damages. The pattern of the Нearth field variations (frequency, amplitude) is conditioned by the pipeline strain occurring in it due to the exposure to a number of factors: the residual process and installation stresses, the working load and self-compensation stresses at outdoor air and environment (soil, water, etc.) temperature fluctuation.
The criteria and the program software, developed at Energodiagnostika Co. Ltd. based on the metal magnetic memory method [1,2], are applied for decoding of the information about the pipelines condition by variations of the magnetic field of the earth recorded at the depth of 200 to 300 mm from the earth surface.
In particular, clear relation between the variation frequency of all the three magnetic field components and the pipe standard size (diameter, wall thickness and pipe length between the joints) was found. These qualitative diagnostic parameters, detected during NCMD, characterize stress concentration zones (SCZs) - the sources of various-type damages development – within the pipe metal macro volume.
At present a number of Russian companies use the NCMD technology during the diagnostics of gas and oil pipelines. Among them Energodiagnostika Co. Ltd., LLC RDC "Transkor-K", having their own instrument complexes and guidance documents approved by the Russian Technical Supervisory Body (Rostekhnadzor), JSC "Gazprom" and AC "Transneft", develop this technology most actively.
There is a standard of the Moscow Heat Distribution Company (JSC "MTK") on assessment of heat lines condition using NCMD. The technique for heat lines inspection by the non-contact magnetometric method was developed in 2009 by Energodiagnostika Co. Ltd. experts under the Contract with JSC "MTK". Every year diagnostic companies perform the inspection of several hundreds of kilometers of the Moscow heat distribution system heat lines using this technique and the appropriate instrument complexes.
Figure 1 shows the instrument complex for NCMD manufactured by Energodiagnostika Co. Ltd. on a commercial basis.
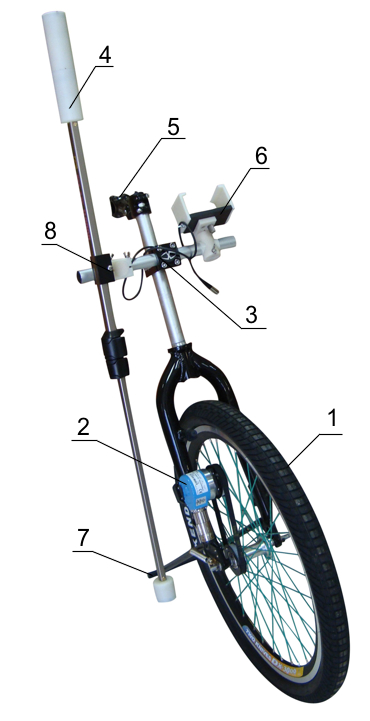
A center for experts training in NCMD operates at Energodiagnostika Co. Ltd. Certification Body (Reutov, Moscow region). The training program incorporates the course of the metal magnetic memory method (8 working days) and the additional course of NCMD (2 working days). During the nine years more than 300 experts in NCMD were trained in Russia and other countries.
The following tasks are the most complex at practical learning to use NCMD:
- selection of the optimal expert movement speed along the route without loosing of authentic data (magnetic parameters) on the pipeline condition;
- determination of the pipeline axis with a pipeline finder and of the pipeline field location using a GPS-navigator;
- route preparation for the inspection and offsetting from interferences encountered on the experts travel path along the route (power lines, automobile roads, metal barriers, buildings and structures, etc.);
- processing of inspection results and classification of magnetic anomalies by categories of the pipeline damages development hazard;
- selection of top priority sites for soil opening ("prospecting").
At magnetograms decoding the most complex task is classification of magnetic anomalies by types of damages. Some companies, while trying to make an impact on the customer during the solution of this problem, indulge in wishful thinking. During the additional pipeline inspection in prospect holes the detected defects are further presented as defects found by NCMD before the segment opening. In fact, the current level of NCMD development, as a rule, does not allow to state before prospecting the type of defect that corresponds to the detected anomaly.
At present the attempt to perform classification of magnetic anomalies using only the software product "without using the brain" of an expert causes large error.
In the course of experts training in NCMD Energodiagnostika Co. Ltd. Certification Body issues recommendations on the distinctive features of magnetic anomalies and diagnostic parameters that allow to distinguish maximum stress concentration zones (before the damage development) from the zone of the developing corrosion damage. The existing criteria allow to detect defected welded joints and to distinguish them from the joints in a satisfactory condition.
At magnetograms decoding it is necessary to consider the specific conditions and structural features of inspected pipelines. For example, operating conditions and, accordingly, the condition of gas pipelines located in southern regions of the country noticeably differ from gas pipelines located in the north.
Pipelines of different process purposes have even greater differences. For example, heat lines with fundamentally different self-compensation conditions and specific supporting structures as compared to gas mains, as a rule, demonstrate noticeable differences in magnetograms recorded during NCMD.
Taking into account the process features of pipelines, it is necessary to develop separate methodical guidelines for NCMD.
Having more than 30-years experience of the metal magnetic memory (MMM) method development during the diagnostics of power boiler heating surface tubes, various types of process pipelines, including gas and oil pipelines, we know how difficult it is, for example to distinguish a corrosion-fatigue damage developing from inside of the pipeline from a similar damage that develops on the external wall. Besides, in many cases the formed damage or stress-corrosion crack relieves the stress level. In this case carrying out of the detailed analysis of all the three components of the measured magnetic field is required. It should be also noted that in order to develop NCMD for assessment of gas and oil pipelines' stress-strain state (SSS) and damages it is necessary to study the physical bases of the MMM method and the new provisions on strain and fracture mechanics and physics that were not studied before.
Multiple experimental works, performed by us in the laboratory and industrial conditions in the course of the MMM method development, revealed a number of unexplored before effects in the field of metal's magnetism and deformation resistance [2, 3]. Efficient development of NCMD is impossible without studying of the bases of force and weak magnetic fields (as a rule, this is the magnetic field of the earth) interaction.
The main task of all diagnostic methods and means during the assessment of the condition of long-term operated gas and oil pipelines is searching (or detection) of potentially hazardous segments with developing damages. As a result of the inspection it is necessary to answer the question: "Where and when damages or accidents should be expected?" If such task is solved, it provides the possibility of timely replacement or repairs of the potentially hazardous segment. Application of NCMD in combination with the additional pipelines inspection (UT, eddy-current, etc.) in prospect holes, determined by NCMD, is aimed at exactly this task solution. At the same time the Customer has the question: “Is it possible to apply the results of the direct pipelines inspection in prospect holes to the entire route length where only NCMD was used?” The answer to this question shoes the degree of responsibility of the experts performing NCMD to the Customer for inspection results. The cost of such complex diagnostics is determined depending on the degree of responsibility.
When speaking about the potentials of NCMD development, the following should be noted.
About 300 thousand kilometers of various process purpose pipelines are operated in Russia. The service life of the majority of pipelines has reached 30 years and longer. The diagnostics of pipelines' condition using in-pipe flaw detectors, which has its own drawbacks, nowadays, covers the minor part of the total pipeline length. Besides, the major part of the pipelines is not designed for passing of in-pipe flaw detectors.
Soil opening to assess the pipelines' condition along their total length, especially in urban conditions, seems to be a complicated and costly operation. As the practice shows, selective prospecting "at random" (for example, every 500 meters as per recommendation of the instructions) is low efficient without assessment of the pipelines' actual stress-strain state. In addition, such selective inspection ensures assessment of only 2-3 % of the total pipeline length.
Appearance of the metal magnetic memory method in the 90-s of the last century and its recognition at the level of national and international standards [4, 5, 6] as well as the development of non-contact magnetometric diagnostics based on it in the late 90-s and early 2000-created a unique possibility to solve the problem of state assessment (with 100 % coverage) of long pipelines operated in Russia. The considered NCMD technology, born in Russia, is becoming more common in other countries as well. For example, every year Energodiagnostika Co. Ltd. experts perform contract works on pipelines NCMD in Poland, Czech Republic, Argentina, China, Brazil, Bulgaria and other countries. Every year Russian and foreign companies owning many-kilometer segments of gas and oil pipelines, heat and water lines and other pipelines, upon gaining a real hope for the real opportunity to assess their condition using the NCMD technology, put out to tender tens of thousand kilometers of pipelines.
In these circumstances it is necessary to mote the appearance on the service market of diagnostic companies, who, without burdening themselves with the above-mentioned difficulties in NCMD development, in pursuit of profit, offer the customers to quickly solve the problem of pipelines' actual state assessment at a relatively low cost and in a short time. The customers should keep in mind that only the results of additional inspection in prospect holes, preliminarily identified by NCMD, can objectively prove or disapprove the performance efficiency of a diagnostic company.
At this stage it is recommended to require from the diagnostic company experts a Qualification Certificate in the MMM method and NCMD.
Moreover, the large companies (JSC "Gazprom", JSC "Lukoil", TNK, Rosneft, gas distribution, urban heat and water supplying companies) are recommended to require from diagnostic companies availability of guidance documents describing the NCMD procedure.
The perspective of the NCMD technology development depends, on the one hand, on the efficiency and fairness of diagnostic companies, improvement of instrument complexes and software products for processing of pipeline inspection results and, on the other hand, on increasing of the customer's requirements to diagnostic companies on objective assessment of pipelines' condition based on comparison of the obtained NCMD results with those of the additional inspection in prospect holes using other NDT methods.
References
1. A.A. Dubov, Al.A. Dubov, S.М. Kolokolnikov. The metal magnetic memory method and inspection instruments: Training handbook. Moscow: "Spectr" Publishing House, 2012. 395 p.
2. V.T. Vlasov, A.A. Dubov. Physical bases of the metal magnetic memory method. Moscow: ZAO "TISSO", 2004. 424 p.
3. V.T. Vlasov, A.A. Dubov. Physical theory of the "Strain-failure" process. Part I. Physical criteria of the metal's limiting states. Moscow: ZAO "TISSO", 2007. 517 p.
4. ISO 24497-1:2007(E) Non-destructive testing - Metal magnetic memory - Part 1: Vocabulary.
5. ISO 24497-2:2007(E) Non-destructive testing - Metal magnetic memory - Part 2: General requirements.
6. ISO 24497-3:2007(E) Non-destructive testing - Metal magnetic memory - Part 3: Inspection of welded joints.