Technical diagnostics and monitoring the condition of equipment and structures at the present stage of development
Dr., Professor A.A. Dubov
The article provides an overview of the state of the art on the topic "Technical diagnostics and condition monitoring of equipment and structures" in Russia and abroad.
Based on author's practical experience of work directly on the equipment, development of Rostekhnadzor guidance documents, Russian and international standards, as well as participation in international organizations and conferences on the considered topic, the experts’ attention is drawn to the problem of limiting state determination of units and components of various inspection objects (IO), starting from the terminology. The "tragedy" of the situation is that all effects of experts working in the field technical diagnostics and monitoring, when assessing the lifetime and risks, are aimed at determination of the limiting state of hazardous industrial facilities (HIF), and till date the normative documents do not contain a clear definition of this concept from the viewpoint of current knowledge of fracture mechanics and materials science.
The article suggests the definition of the concepts like the limiting state of metal in a local area of a structure and limiting state of the structural member itself based on the carried out study of the "strain - failure" process [1]. The necessity to implement the recommendations of current national standards in the development of regulatory documents (safety guidelines) and in performing technical diagnostics and assessment of HIF lifetime is noted. In particular, the paper points out the necessity to carry out the actual stress-strain state control and to detect local SCZs determining the performance of any IO.
To solve scientific-technical, methodological and organizational problems on the considered topic, it is proposed to combine efforts of RSNDTTD, Rostekhnadzor, Federal Agency for Technical Regulation and Metrology (Rosstandart), as well as of non-governmental organizations like SIU RISCOM.
At present technical diagnostics, lifetime and risks assessment and equipment and structures condition monitoring gain more and more development in Russia and in other countries of the world.
In the foreign community the most active work on the topic "Technical Diagnostics and Monitoring" has been carried out since 1988 by the international organization "Condition Monitoring and Diagnostic Engineering Management" (COMADEM). Every year, the international congress on exchange of experience between scientists and practicians from different countries working in this area is held on the initiative of COMADEM management. Representatives of SPC "Dynamics" (Omsk) and Energodiagnostika Co. Ltd. (Moscow) periodically participate in the congresses held by COMADEM on behalf of Russia.
On August 20-22, 2016, Xi'an (China) hosted the 29th Congress of "COMADEM-2016", which was attended by about 300 experts (scientists and practicians) from 20 countries (Australia, USA, UK, Canada, New Zealand, China, Russia, Japan, etc.). General Director of Energodiagnostika Co. Ltd. A.A. Dubov took part in the work of "COMADEM-2016" congress on behalf of Russia at the invitation of the Chinese organizers. He presented a plenary paper on the topic: "Energodiagnostics - the physical basis of the metal magnetic memory method".
It should be noted that the main objective of the congresses held by COMADEM is the exchange of experience between specialists from different countries in the field of development of various techniques and procedures of information systems (IT technologies), integrated controls and monitoring in various industries.
In the field of technical diagnostics within the COMADEM framework achievements in vibration diagnostics were mainly discussed till date. As it is well known, problems and achievements in the field of diagnosing directly the metal state of equipment and structures are discussed and regulated by the International Committee for Non-Destructive Testing (ICNDT) and relevant regional federations.
In 2015, as a result of an agreement between ICNDT and the International Society for Condition Monitoring (ISCM), a Work Group "Condition Monitoring and Diagnostic Technologies" was formed. The main objective of this Work Group is generalization of the world experience on the above topic, development of international standards, preparation of experts training programs, holding of international workshops and conferences.
The Work Group plan outlines the following basic tools for direction development on the topic "monitoring and technical diagnostics":
- instrumentation control (various methods and devices for technical diagnostics);
- computational methods (strength calculations, lifetime and risks assessment).
ICNDT Work Group and the British Institute of non-destructive testing (BINDT) plan to hold the first international congress on the topic "Condition Monitoring" in the UK in 2017.
In Russia there is a scientific-production union "RISCOM" - an organization uniting the efforts of a number of diagnostic companies and scientists of the Russian Academy of Sciences. The Committee for Technical Diagnostics (TK-132) has been operating for already dozens of years at Rosstandart, the basic activities of which are: standardization in the field of vibration diagnostics, stress control, strength, non-destructive testing, physical and mechanical characteristics of the metal, etc.
The Coordination Council "Stress-strain state control and lifetime assessment" was formed in 2003 at the initiative of TC-132 experts. General Director of Energodiagnostika Co. Ltd. Prof. A.A. Dubov was approved as Chairman of this Council.
During the period from 2003 to 2015 more than 10 up-to-date Russian standards on "Stress control and lifetime assessment" were developed at TC-132, most of which are "pioneer" and have no analogues in the world.
In 2015, at SIU "RISCOM" initiative, the TC-227 "Monitoring of complex engineering systems" was found and started its work at Rosstandart. The ideological basis of SIU "RISCOM" and the mentioned Rosstandart technical committees is the development of methodology and standards in the field of monitoring, risk assessment, technical diagnostics of complex engineering systems.
Instrumental methods of technical diagnostics that meet the objectives of monitoring, lifetime and risks assessment are:
- acoustic emission method (AE);
- metal magnetic memory (MMM) method;
- thermal control;
- vibration diagnostics;
- stress control methods.
The listed above and other NDT methods can be used effectively in a complex combination, for example, SPC "Dynamics" system of integrated monitoring for accident prevention and state control (COMPACS) uses a number of NDT methods: vibration, AE, thermal, electrical, eddy current, optical.
In March 2016, in accordance with the decision of Rostekhnadzor STC Section on security of oil and gas complex facilities, a committee on technical diagnostics headed by the Chairman - IC "Rustehekspertiza" General Director Prof. B.P. Tumanyan - was found.
The Committee developed federal rules and regulations in the field of industrial safety "Basic requirements for technical diagnostics of engineering devices, buildings and structures at hazardous industrial facilities".
Currently the draft of this document passed the expert review at a number of oil and gas industry enterprises and organizations including JSC "Giproniigaz", SRIIN ISPU "Spektr", PJSC "Gazprom", OJSC "Gazprom neftekhim", JSC NIICHIMMASH, OJSC "Rosneft Oil Company", CJSC "GIAP-DISTcentr" and others.
Based on the results of full-time discussion of the said document, the first item of the Meeting Minutes wrote: "To recognize the work of the Committee as important and perspective". In accordance with federal rules and regulations (PB) "Basic requirements for technical diagnostics at hazardous industrial facilities", in the coming years it will be required to revise old guidance documents (GD) for monitoring and assessment of pipelines, vessels and other equipment lifetime in order to develop Safety Manuals (RB) taking into account the requirements specified in FNiP (Federal rules and regulations).
Technical diagnostics is a higher level of HIF reliability and safety assurance compared to conventional methods of non-destructive testing and flaw detection. According to FNiP, the term "technical diagnostics" means determination of an object's technical condition. This definition is taken from the old GOST 20911-89 "Technical diagnostics". This GOST states that the main objectives of the technical diagnostics are:
- monitoring the technical condition by various methods and means of non-destructive and destructive testing;
- search for locations and causes of failures (malfunctions);
- prediction of technical condition.
In accordance with GOST 20911-89, prediction of technical condition is aimed at determination with pre-specified probability of the time (service life) interval, within which the object's performance is ensured.
Thus, in short, the objective of inspection object (IO) technical diagnostics is assessment of the technical condition and service life extension for a certain period of safe operation (at least for a period between overhauls).
In this regard, it should be noted that in 2008 Energodiagnostika Co. Ltd. experts jointly with Rosstandart TC-132 prepared and approved GOST R 53006-2008 "Lifetime assessment of potentially hazardous facilities based on express methods. General requirements".
Figure 1 shows the block diagram of equipment residual lifetime determination using the express methods of non-destructive testing (NDT).
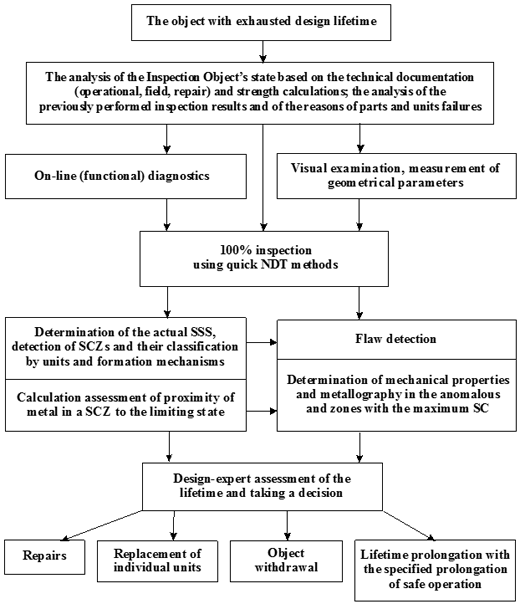
Passive NDT methods that use the internal energy of the structures metal are referred to express methods:
- acoustic emission method (AE);
- metal magnetic memory (MMM) method;
- thermal control.
At present these methods have become the most widespread in practice for early diagnostics of equipment and structures damaging. The fundamental difference of such an approach to the lifetime assessment is performance of the 100% IO examination with detection of all potentially hazardous stress concentration zones (SCZs) - the sources of damages occurrence during the equipment operation.
The new national standard GOST R 53006-2008 highlights the following basic provisions:
- it is proposed to use the actual energy characteristics, which can be determined by the MMM method, AE and thermal method, as the main criteria of the metal's limiting state;
- structural diagram for residual life estimation with a focus on up-to-date express methods of technical diagnostics is proposed;
- it is suggested to perform calibration strength calculations with residual life assessment for operated SCZs taking into account the actual structural-mechanical properties of the metal, determined during the inspection.
Here it should be noted that during the revision of guidance documents, required in accordance with Rostekhnadzor FNiP requirements for performing technical diagnostics, it will be necessary to take into account the recommendation of GOST R 53006-2008 and other up-to-date standards in the field of stress control. In 2010 at the initiative of a number of training centers (STC "Quality" LLC, Energodiagnostika Co. Ltd., CJSC "DIGAZ") OJSC “STC "Industrial Safety" supported by RSNTTD developed and put into effect the guidance document SDOS-05-2010 "Regulations on certification of personnel in the field of stress-strain state non-destructive testing". In accordance with the mentioned guidance document, since 2010 experts have been trained and certified in the field of stress control under special programs at STC "Quality" LLC and Energodiagnostika Co. Ltd.
It is obvious that after approval of Rostekhnadzor FNiP on technical diagnostics it will be required to organize the system of experts training in the field of technical diagnostics and monitoring.
Technical diagnostics and monitoring is a higher level of development in relation to the system of non-destructive testing (NDT), and experts in this field should have comprehensive knowledge. Such expert should know the following: the advantages and drawbacks of various methods and means of destructive and non-destructive testing including methods of stress control, materials science and destruction mechanisms, methods of strength estimation and prediction. For rotating machinery such expert must understand the issues of vibration diagnostics. And, of course, such expert must know the current guidance documents of Rostekhnadzor, national standards and enterprise standards of the industry, in which he works. Experts of the highest category (in accordance with the old certification system) have this knowledge to some extent. However, to the author's opinion, experts in the field of technical diagnostics and monitoring require special training.
During the technical condition assessment of hazardous industrial facilities (HIF), despite the fact that at present Rostekhnadzor conventionally divided them into four classes of hazard, it will be necessary to use common assessment criteria. One of the most important criteria for technical condition assessment of long-term operated HIF is the criterion of the "limiting state". Currently, the majority of Rostekhnadzor guidance documents developed by branch institutes in the 90s of the last century and in the early 2000s provide, as a rule, the following general definition in lifetime assessment of HIF: "limiting state is the state of inspection object, at which performance is deteriorated and its further operation is impractical".
However, experts in fracture mechanics know that any inspection object material's capability to resist external loads is determined by the remaining margin of the material's self-energy in the local area, which turned out to be in the least favorable position with bad combination of design features and operating conditions, i.e. in the area with the highest self-energy input for resistance to workload. And from this it clearly follows that first of all it is necessary to know where this area is located. For example, passive methods - the metal magnetic memory method, acoustic emission, thermal control that use their internal self-energy of the material radiated by IO - are most efficient for the detection of these local areas that determine performance of any IO.
Scientific substantiation of the metal's limiting state from the standpoint of modern fracture mechanics [1] is provided specifically for such local areas. The limiting state of the metal in a local area occurs at achieving the physical tensile strength when, as a rule, a microcrack forms on the metal surface and the damage development begins. In experimental studies have found that the level of stress in local SCZs with sizes ranging from tens of micrometers to a few millimeters, may significantly exceed not only the yield strength but also the tensile strength of the metal. In this state of the metal the structural element, taking into account safety factors, can still work for a long time.
The limiting state of a structural element occurs in conditions when the developing damage area of the metal becomes comparable with the size of the structural element itself.
As it can be seen, the material's limiting state criteria obtained by simple mechanical testing of specimens (conditional yield strength and tensile strength), cannot reflect the limiting state of the material and, moreover, the limiting state of a structural element. Experience of 100% inspection of various equipment, pipelines, structures, rotating machinery using the MMM method shows that only 5-10% of the total volume of the metal face the development of defects in SCZs after the long-term equipment operation. However, as a rule, the locations of local SCZs formation and the level of metal degradation in these zones are not known.
The research results presented in the paper [1] indicate the necessity to develop new regulatory documents governing the procedure of certification of devices for equipment and structures' stressed-strained state diagnostics.
From the standpoint of modern knowledge in the field of fracture mechanics and materials science about the metal's and structural element's limiting state, it is also necessary to develop new regulatory documents on technical diagnostics, monitoring and HIF lifetime and risk assessment.
In conditions when it becomes possible, using the MMM method, to perform 100% equipment inspection and to identify all potentially hazardous zones, susceptible to damages development, lifetime and risk assessment becomes more specific and predictable [2].
In conclusion it should be noted that, despite the stagnation of the economy, we are currently experiencing in Russia insufficient demand and interest to the topic "Technical Diagnostics and Monitoring" on the part of the industry. This direction of work in the field of HIF industrial safety assurance is being actively developed by Russian experts (scientists and practicians). And we occupy a leading position in the field of methodology and standardization compared to the state of the art in relation to this topic in other countries of the world.
For example, this article notes that our national standards on "Stress-strain state control of HIF" are "pioneer" and have no analogues in the world. Some scientific-technical, methodological and organizational problems that currently exist in Russia with regard to the considered topic require combining the efforts of RSNTTD, Rostekhnadzor, Rosstandart (TC 132, TC 227, TC 361, and other committees), as well as of public organizations like SIU "RISCOM".
References
1. V.T. Vlasov, A.A. Dubov. Physical theory of the "strain-failure" process. Part I. Moscow: ZAO "Tisso", 2007. 517 p.
2. A.A. Dubov. Monitoring of risks based on early diagnostics of equipment and structures metal state in stress concentration zones - sources of damages development // Himicheskaya tekhnika. 2016. No.4. pp. 26-28.