Determination of metal's mechanical properties by hardness parameters in stress concentration zones detected in engineering products using the metal magnetic memory method
V.M. Matunin (Moscow Power Engineering Institute)
A.A. Dubov, Al.A. Dubov (Energodiagnostika Co. Ltd.)
At present all leading diagnostic centers of the world are occupied with the problem of stresses and strains control in operated structures in order to assess their state. However, it is known that effectiveness of stress inspection methods remains low during their practical application. Improvement of the efficiency of technical objects' stress-strained state (SSS) non-destructive testing (NDT) during their lifetime assessment gains special importance.
At present a large arsenal of methods and means for non-destructive testing of residual stresses (RS) in engineering products and for control of operated industrial plants' stress-strain state (SSS). However many administrative and scientific-technical problems occur during their practical application. The following problems are among them:
- lack of metrological basis for certification and calibration of products' SSS characteristics measurement means (till date there are no unified standards and samples in Russia and other countries);
- unsuitability of most of the methods for inspection of long pipelines and large-sized products, equipment and vessels;
- impossibility to assess the SSS of the metal's depth layers in products;
- insufficient development of programs and centers for experts training in the field of SSS NDT;
- lack of guidance documents specifying general requirements to methods and means of stresses and strains NDT in real structures.
The standard specifying general requirements in relation to the topic of SSS NDT was first developed in Russia by the experts of Energodiagnostika Co. Ltd. jointly with TC 132 of the Federal Agency for Technical Regulation and Metrology (Rostekhregulirovanie). It was published in 2005 as GOST R 52330-2005 "Non-destructive testing. Stressed-strain state test on industrial objects and transport. General requirements".
It is known that stress concentration zones (SCZs), occurring due to manufacturing process defects, working loads or their combinations, are main sources of equipment damaging. Presence of SCZs both on new and used products sufficiently reduces their lifetime. Therefore GOST R 52330-2005 specifies control of products' stress-strained state and SCZs detection using non-destructive devices as the most important task during the SSS control. It is suggested to use the metal magnetic memory (MMM) method, which gains more and more practical implementation, to solve exactly this problem – SCZs detection based on the 100% inspection of equipment and structures.
After detection of SCZ the lifetime assessment requires determination of the metal's mechanical properties in these zones. However determination of the metal's mechanical properties in small-area (from few to several tens of microns) SCZs is rather problematic.
The indentation method is the most perspective among the existing methods of mechanical properties testing. This method known as a "non-standard method" allows to determine not only hardness characteristics but also the indices of other mechanical properties of the metal like the yield strength (σ0.2), ultimate strength (σult), uniform strain (dun) and others [1]. The “non-standard method” is based on the correlation relationship of hardness characteristics with strength characteristics. But these relationships were established for the macro level where the deformed metal volumes during the indenter indentation and the specimen tension are comparatively large. When the deformed metal volumes are decreased, the scale factor starts exhibiting itself, which results in increase of the determined hardness and strength values. For small-area SCZs it is possible to apply only the method of micro hardness determined by a pyramid indentation. However the micro hardness values may exceed the macro hardness values by 1.5 or 2 times due to the scale factor influence.
The same increase of hardness occurs during the hardness tester ball (spherical indenter) indentation as well. The smaller the indenter's diameter is, the higher the Brinell hardness is provided that the indentation diameter to the indenter's diameter ratio is constant [2].
The scale factor has similar influence on the strength characteristics determined by means of specimens tension. Sufficient increase of tensile specimens' strength with diameter less than 1mm was reported.
The above said prompts a question on the nature of hardness to strength relation at the micro- and macro level as well as on the possibility of their interconversion. To provide a substantiated reply to this question it is necessary to know the regularities of hardness and strength characteristics variation during transition from macro to micro level of the metal strain.
To answer these questions special tensile and indentation tests on specimens made of the same steel grade were carried out at the MEI "Metals Technology" Chair laboratory. Two similarity conditions were revealed as a result of the experiments performed. The first condition ensures identical scale levels during tension and indentation due to equality of absolute variation of the specimen's cross section area ΔF and the indentation surface area М (ΔF=M). And the second condition ensures equality of relative strains during the specimen tension Ψtens and the indenter indentation ψind (ψtens=ψind). To fulfill these conditions it is appropriate to use a hardness tester ball (spherical indenter), which allows to obtain various plastic strain values due to the indentation angle variation in the course of one loading.
For quantitative evaluation of average plastic strain during the hardness tester ball indentation ψind the following formula is suggested [3]:
ψind=1-[1-(d/D)2 ]1/2=0.5t/D=t/R , (1)
where d – indentation diameter; t – indentation depth; D – indenter's diameter; R – indenter bending radius.
The suggested similarity conditions and formula (1) allow selecting the required initial diameter of the tensile specimen dо by the used indenter's diameter D.
A 20 mm diameter rod made of steel 35 was takes as a material for investigations. Test nuts for indentation test and dies for making tensile specimens were cut from the rod. Spherical indenters with diameters D=0.1–10 mm and cylindrical quintuple tensile specimens with initial diameters dо=0.6–10 mm were made to perform mechanical tests.
Tensile testing of specimens was carried out using the Instron multi-purpose machine that allows variation of load scales depending on dо. During tension of various-diameter specimens the yield strength σ0.2, ultimate strength σult and absolute variations of the specimens' cross-section area were determined at the level of the yield strength ΔF0.2 and at the level of at the level of ΔFult.
Testing by means of various-diameter indenters indentation were carried out using the modernized instrument MEI-T7 equipped with integrated microscope for measuring of indentation diameters and replaceable power springs to ensure the required load measuring accuracy. The instrument's design allows to indent the indenter into the same point with gradual load increase and indentation diameter measurement at each loading stage. As a result of such testing it is possible to obtain an indentation chart. During indentation of various-diameter indenters hardness at the yield strength level НВ0.2 and indentation surface М0.2, corresponding to it, hardness at the ultimate strength level НВult and indentation surface Мult corresponding to it were determined. The technique for НВ0.2 and НВult determination is described in [3].
The results of tensile and indentation testing of the metal showed that if the suggested similarity conditions are fulfilled, the ratios σ0.2/НВ0.2 and σult/НВult remain the same at the macro and micro levels and are equal approximately to 1/3. These similarities are conditioned by the equality of strain energies occurring during the specimen tension and the indenter indentation because resistance to external load during both types of testing represents simultaneously force-torque and strain components that cumulatively form the resistance energy [4]. This is how the physical sense of the "stress-strain state" concept is displayed.
Figure 1 shows experimental dependencies of σ0.2, σult on dо and НВ0.2, and of НВult on D obtained based on tensile testing of 0.6 to 10 mm diameter specimens and 150 to 350 microns diameter steel wire specimens with preliminary annealing to remove cold-work as well as on indentation of various-diameter indenters (0.1 to 10 mm).
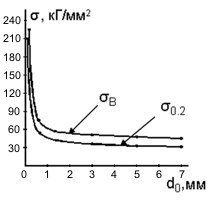
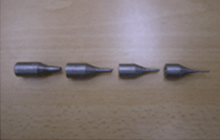
Figure 1a. Variations of σ0.2 and σult depending on dо.
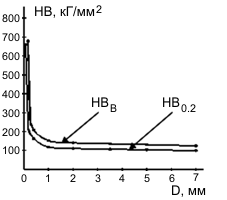
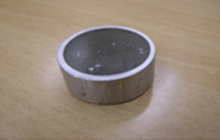
Figure 1b. Variations of НВ0.2 and of НВult depending on D.
For indentation testing of wire specimens special micro sections were made. To do it wire segments were placed in a cylindrical metallic fixture (figure 1, b) filled with heated and softened polystyrol. Longitudinal axes of segments were kept perpendicular to the fixture base. After polystyrol hardening the wire butt ends located in the same plane were milled, ground and polished. Such preparation allowed to indent small-diameter indenters into the wire segment butt ends (figure 1). An indenter with bending radius at the top R=0.05 mm (D= 0.1 mm) was used for this purpose. Figure 1 demonstrated clear similarity in strength and hardness characteristics variations, which is the evidence of general regularities of the scale factor influence during transition from the macro to the micro level of metal strain. It should be noted that for wire specimens the values of σ0.2/НВ0.2 and σult/НВult ratios also turned out to be approximately equal to 1/3.
Significant increase of hardness characteristics can be observed in the segment of dependencies НВ0.2=f(D) and НВult=f(D) at D<1 mm. Similar increase of hardness characteristics can be also observed for dependencies σ0.2=f(dо) and σult=f(dо) at dо<1 mm. The experimental data analysis showed that these segments can be approximated using exponential dependencies. Thus, for example, dependencies of hardness characteristics НВ0.2 and НВult on D may be represented as follows:
НВ0.2=Аexp(-aD); НВult=Вexp(-bD), (2)
where А, a, В, b - are fixed factors for a specific material.
To determine the factors making part of the dependencies (2) it is sufficient to determine two values of НВ0.2 (НВ0.2I and НВ0.2II) and two values of НВult (НВultI and НВultII) during indentation of two indenters with different diameters (DI and DII):
a = [ln (НВ0.2I/ НВ0.2II)] / (DII - DI);
b = [ln (НВultI/НВultII)] / (DII - DI); (3)
А =НВ0.2I/ exp(-aDI);
B =НВultI/ exp(-bDI). (4)
Experiments and calculations showed that indenters with diameters DI=0.4 mm and DII=1 mm can be used for metal testing in SCZs with length of at least 200 microns. If the length of SCZs is less, smaller diameter indenters are required.
Knowing the factors А, a, В, b it is possible to calculate the values of hardness characteristics for the indenter's diameter D that would correspond to the required tensile specimen's dо. In this case it is possible to convert hardness characteristics НВ0.2 and НВult to strength characteristics σ0.2 and σult using the dependencies presented in figure 1.
It is known that the ratio σ0.2/σult is a diagnostic parameter of the SCZ metal's structural-mechanical state by the MMM method. If this ration is within the range of 0.5 to 0.8, then the metal is not yet susceptible to brittle fracture, and the probability of cracks initiation is low. However when this ratio increases and verges towards the unit value the metal exhausts the hardenability margin, its uniform strain is very low, and therefore the controlled SCZ is of serious hazard because it might become a site of cracks formation. In this case the data on the metal's state in the SCZ should be supplemented with metallographic analysis using the plastic replication method.
Table 1 presents the results of the SCZ metal's mechanical properties diagnostics in the turbine blade made of steel 20Cr13. The length of this zone was approximately 750 microns. To determine the mechanical properties by the indentation method 0.4 mm and 1 mm diameter indenters were used. The table presents not only the indenters' diameters D but also the specimens' diameters dо, to which σ0.2 and σult correspond during tension according to the suggested similarity conditions.
Table 1
Results of the metal's mechanical properties determination inside and outside SCZ of the turbine blade
Mechanical properties | Metal in SCZ | Metal outside SCZ | ||
---|---|---|---|---|
DI = 0,4mm dо = 0,6mm |
DII = 1,0mm dо = 1,4mm |
D = 2,5mm dо = 3,5mm |
D = 2,5mm dо = 3,5mm |
|
НВ0,2, kg/mm2 | 348 | 351 | 298 | 270 |
НВult, kg/mm2 | 375 | 351 | 298 | 270 |
σ0,2, kg/mm2 | 114,8 | 107,3 | 90,4 | 72,6 |
σult, kg/mm2 | 123,8 | 115,8 | 98,3 | 89,1 |
σ0,2/ σult | 0,927 | 0,926 | 0,920 | 0,810 |
As it follows from table 1, the metal in SCZ is characterized by the high ratio σ0.2/ σult; therefore it is potentially dangerous due to the probability of cracks formation.
Figure 2 presents the results of the stud inspection (⌀ 60 mm, steel EP182) by the MMM method. This stud had been in operation for about 30 years on the flange joint of the PT-60-130 turbine generator high pressure cylinder. Figure 2, a shows the inspection scheme of the stud from the SCZ detected by the MMM method. Figure 2, b shows the distribution of the normal component of the magnetic Н field and its gradient along the lateral surface of the stud where the maximum values of the field gradient dH/dx characterizing the SCZ were recorded.
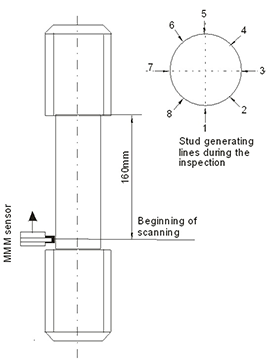
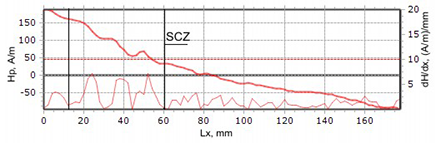
Then hardness measurements and determination of the stud metal's mechanical properties in SCZ of this stud were performed using the instrument complex MEI-T7 (figure 3). Table 2 presents the stud metal's mechanical properties in SCZ and outside this zone. It should be noted here that, based on the experience of inspection by the MMM method of studs located on flange joints of turbine generator cylinders, cases of SCZs detection on lateral generating lines of studs are quite frequent. These are exactly the SCZs where damages development in the course of operation should be expected. However, in accordance with the guidance document [5] effective in the Electric Power industry, it is recommended to control the studs' hardness on butt ends considering that studs work in tension based on calculations.
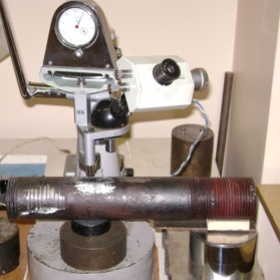
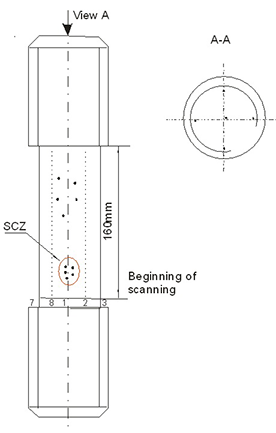
Table 2
Results of the stud metal's mechanical properties determination inside and outside the SCZ
Mechanical properties | in SCZ | outside SCZ |
on stud butt end (average values) |
---|---|---|---|
D = 1,0mm | D = 1,0mm | ||
σ0,2, MPa | 810 | 570 | 604 |
σult, MPa | 980 | 750 | 788 |
δpr, % | 5,6 | 7,4 | 7,1 |
НВ | 297 | 233 | 238 |
σ0.2/ σult | 0.826 | 0.76 | 0.768 |
δpr, % - relative proportional elongation.
It can be seen in table 2 that this stud metal's mechanical properties obtained during measurements on the butt end are in a satisfactory condition and conform to the norms (GOST 20072-74). At the same time the metal's strength characteristics measured in the SCZ detected by the MMM method have values exceeding the permissible limit.
It should be also noted here that the values of σ0.2 and σult obtained based on the results of hardness characteristics measurement in the stud SCZ depend on the level of residual stresses (RS) in this zone. The higher the RS level is, the higher the values of hardness and other mechanical characteristics will be obtained as a result of the above-mentioned measurements. At the same time assessment of the RS level in SCZ can be made by the MMM method using the energy ratio between the magnetic and the mechanical characteristics presented in the paper [6].
References
1. M.P. Markovets. Determination of metals' mechanical properties by hardness. Moscow: Mashinostroenie, 1979. 191 p.
2. V.M. Matunin, A.N. Demidov, M.A. Prokhodtsov, B.A. Uzikov. Scale factor influence on the results of Brinell hardness test // Technology of metals, 2008, No.8. pp. 49-52.
3. V.M. Matunin. On-line diagnostics of mechanical properties of structural materials. Moscow: MEI Publishing House, 2006. 214 p.
4. V.T. Vlasov, A.A. Dubov. Physical Theory of the "Strain - Failure" Process. Part I. Physical criteria of metal's limiting states. Moscow: ZAO "Tisso", 2007. 517 p.
5. GD 10-577-03. Standard instruction for metal control and boilers, turbines and pipelines main units' service life extension at thermal power stations. Moscow: JSC "STC "Industrial Safety", 2007.
6. A.A. Dubov, Al.A. Dubov, S.M. Kolokolnikov. Metal magnetic memory method and inspection instruments: Training handbook - 5th edition. Moscow: Publishing House "Spektr", 2012. 395 p.