Integrated testing of liquid ammonia refrigerator tank welded joints
A.A. Dubov, S.M. Kolokolnikov (Energodiagnostika Co. Ltd.)
A.G. Medvedev, D.S. Boriskin (KJSC "Azot")
Refrigerator tanks (RT) for storage of liquefied gases are one of the most hazardous industrial facilities (HIF), where accidents with serious consequences occur.
Defects of welded joints are one of the main causes of RT emergencies [1]. In this connection, special attention is paid to RT welded joints quality control, especially in the area of the tank bottom and the first shell rings to the height of up to 10 m [2].
In accordance with [2], the main non-destructive testing (NDT) method in the technical inspection of a vertical steel refrigerator tank is acoustic emission (AE). Other NDT methods (visual instrumentation control (VIC), ultrasonic testing (UT), dye penetrant inspection (DPI), etc.) are considered as additional and are applied on the internal shell in places with increased activity of detected AE sources in order to determine the actual location of defects.
If it is impossible to carry out AE inspection, conventional NDT methods are applied in the scope specified in the guideline [2] and on the basis of visual inspection. The above NDT methods, specified in [2], are aimed at detection of developed defects occurred in the course of installation and operation, and do not provide an assessment of the stress-strain state (SSS). In accordance with the guidelines [2], to solve this problem, application of the metal magnetic memory (MMM) method is recommended.
The MMM method is a passive magnetic method based on recording and analysis of the intensity distribution of the self-magnetic stray fields (SMSF) formed in the course of fabrication (welding) or during operation of ferromagnetic products under the action of workloads and a weak geomagnetic field [3, 4]. In the course of theoretical and experimental research, it was found that SMSF distribution characterizes the inspection object's SSS.
In accordance with [2], it is allowed to perform inspection by the MMM method in the scope amounting up to 30% of all NDT work, or inspection of all RT internal shell wall welds located at a height of more than 10 m.
Let us consider the experience of the MMM method application in combination with ultrasonic testing of welded joints of a refrigerator tank installed in the ammonia transportation shop at Kemerovo Joint-Stock Company (KJSC) "Azot".
KJSC "AZOT" ammonia transportation shop RT refers to "full containment" RTs and is a structure consisting of two tanks — the internal one, where the liquefied gas is directly stored, and the external one. The external tank protects the insulation against damaging and moisture penetration.
An integrated NDT with application of the MMM method and UT of a double-walled RT was performed by the strength control area experts of KJSC "Azot" HIF technical diagnostics shop in August 2016.
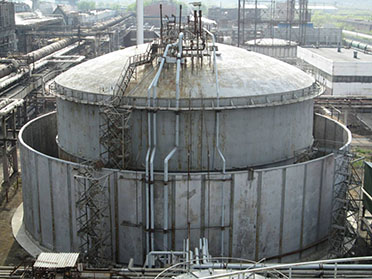
First, the following RT internal shell welded joints were inspected using the MMM method:
- bottom edge welds (double fillet T-joints, butt joints, lap joints);
- bottom longitudinal welds (butt joints, lap joints);
- bottom transverse welds (butt joints, lap joints);
- the first wall ring welds (butt joints).
During the RT welds inspection by the MMM method, a scheme of measuring two SMSF (H) intensity components (normal and longitudinal tangential) was used in accordance with [5].
In the course of inspection by the MMM method, SCZs characterized by anomalous distribution of the H field intensity with maximum and average gradient values dH/dx were observed on each standard size of welded joints.
UT was performed in individual SCZs with maximum and average field gradient values in order to determine the field gradient limiting value, at which unacceptable defects in accordance with the UT standards were recorded.
Further, UT was carried out on all welded joints in SCZs with limiting and higher values of the field gradient H.
Inspection by the MMM method resulted in detection of a total of 115 SCZs with field gradient values exceeding the limiting value. The UT detected discontinuity flaws in all 115 SCZs, and in 104 SCZs the detected discontinuity flaws were unacceptable in accordance with the standards [6]. Thus, in all 115 detected SCZs the UT confirmed the 100% reproducibility of the MMM inspection results with location of the weld material discontinuity flaws. At the same time, reproducibility of the MMM and UT method results for unacceptable defects location was 90.4%.
It should be particularly noted that 1046 meters of RT welds were inspection in this way, and the total length of detected SCZs with defects confirmed by the UT amounted to 11.3 meters, that is, only 1.08% of the total scope of inspection.
The results of an integrated inspection by the MMM and UT methods are currently used on all RTs and other KJSC "AZOT" HIF.
References
1. H.M. Khanukhov. Analysis of causes of steel tanks emergencies and improving the safety of their operation // Chemical and oil and gas engineering, No. 10, 2003. pp. 49-52.
2. GD 03-410-01. Guidelines for performing an integrated technical inspection of liquefied gas refrigerator tanks.
3. A.A. Dubov. Fundamental distinguishing features of the metal magnetic memory method and inspection instruments compared to known magnetic methods of non-destructive testing // Control. Diagnostics, No. 12, 2003. pp. 27-29.
4. S.M. Kolokolnikov. Determination of the weld metal mechanical properties by hardness parameters in stress concentration zones detected by the metal magnetic memory method // Welding production, No. 12, 2013. pp. 31-38.
5. GOST R ISO 24497-3-2009. Non-destructive testing. Metal magnetic memory method. Part 3. Inspection of welded joints.
6. STO 00220256-005-2005. Welds of pressure vessels and units butt, fillet and T-welded joints. Ultrasonic Testing Technique.