Metal magnetic memory method and its capabilities for diagnostics of power boiler elements
Dr., Professor A.A. Dubov
The article considers the reasons of boiler tubes damaging and the existing problems in the diagnostics of these damages at an early stage of their development. Capabilities of the metal magnetic memory method for early diagnostics of developing damages of steam pipes and power boiler waterwall tube bends are presented.
Zones of mechanical stress concentrations (SCZs), in which corrosion, fatigue and creep processes flow the most intensively, are the main sources of heating surface (HS) pipes failure. Stress concentration on some sections is mainly caused by insufficient pipes self-compensation and occurs due to various deviations from the design pipes movement in movable fittings accepted at boilers installation and repairs; increasing of thermal-hydraulic sweep; incorrect installation of repair inserts; pipes jams in repair "dies" and in sites of pipes and coils passing through setting. Timely detection of pipe sections with maximum stress concentration is the main task solved by the diagnostic method based on the metal magnetic memory (MMM) effect.
International ISO Standards on the MMM method 24497-1:2007(Е), 24497-2:2007(Е) and 24497-3:2007(Е) are published. Based on the international standards, national standards were put into effect in Russia, Ukraine, Poland, China, Mongolia, and Iran. In Russia the Russian Technical Supervisory Body (Rostekhnadzor) included the MMM method in the list of basic non-destructive testing methods recommended for application at hazardous industrial facilities (HIF). More than 50 Rostekhnadzor guidance documents for various industries are currently effective, recommending the MMM method for inspection of pipelines, vessels, equipment and structures. TUV Rheinland Inter Cert Kft Certificate (01202 HU/V 11-3420) permitting the MMM method application at HIF was obtained in 2011.
It is known that tubes in "as delivered" condition have a certain level of residual magnetization. In installation conditions the residual magnetization varies and re-distributes under the influence of welding and installation stresses. At operating of boiler tubes the residual magnetization formed during fabrication and installation changes under the effect of working loads.
It was established in the course of special laboratory and industrial testing that re-distribution of residual magnetization and of self-magnetic leakage field (SMLF) Н respectively on the pipes surface is caused by the action of the magnetoelastic and magnetomechanical effects. It was also established that variation of residual magnetization and of the measured field Н respectively at tensile, compression, torque and cyclic loading of ferromagnetic pipes is unambiguously associated with the maximum action of operating stresses, which allowed using this parameter as a memory element at development of this diagnostic method.
It is known that pipes stability loss occurs at axial force approaching the critical load value. An elastic pipe deflection occurs, which disappears after axial load relief.
In conditions of a boiler pipe operation a bend with torque occurs, as a rule, on a section with insufficient self-compensation (for example, at jamming in fitting units) at stability loss. An appropriate stress field and shear planes with maximum metal strain occur in the weakened area of such pipe section. Stable slipbands and glide pads appear in the same zone on the pipe surface long before approaching the conventional yield strength of metal. Stable slipbands also occur in cases of local metal overheating due to the lack of self-compensation along the pipe perimeter and wall thickness. The moment of stable glide pads occurrence is associated with internal stresses (tensile or compression stresses) level and orientation. Stable dislocation slipbands, occurring under the influence of repeating in the same place cyclic loads, may develop to channels up to tens and hundreds of microns in depth and width, which will be already visible at the macro level. Development of plastic strain and, as a result, cracks initiation takes place along these channels boundaries.
The many-years experience in magnetic field investigation on boiler and steam pipes revealed presence of stable lines of the Н field intensity normal component's sign alternation in zones of developing metal damages (Н=0 lines). Interpretation of this diagnostic magnetic parameter as the main stresses line occurring on pipes surface under the influence of operating loads is confirmed by design investigations [2, 3]. It is obvious that coincidence of Н=0 lines with welded joints and bends is most dangerous for HS pipes reliability.
For quantitative estimation of stress concentration level the Н magnetic field normal and/or tangential component's gradient (variation intensity) is determined [4]:
Кin=|ΔHр|/Δx (1)
where Кin - is the magnetic leakage field gradient characterized by the intensity of metal magnetization in stress concentration zone (SCZ) and by the Н field variation intensity, respectively; |ΔH| - is the modulus of the Н field difference between the two points of inspection; Δx – is the distance between the two points of inspection.
The suggested in the technique criteria allow distinguishing pipe sections operating in the zone of metal elastic strain from sections operating in the zone of metal plastic strain and being in the metal pre-failure state.
As a rule, zero lines of the normal component of the magnetic field (Н=0 lines) correspond to stress concentration zones, being the sources of damages development. However, in some cases of developed local defects (for instance, corrosion pits) the local variation of the Н field takes place without sign alternation. The common feature of SCZs and developed defects is an abrupt local variation of the Н field and its gradient Кin. Zones of maximum SC correspond to zones with maximum values of field gradients Кin.
The considered magnetic method of heating surfaces (HS) diagnostics can be used independently and in combination with other destructive and non-destructive inspection methods.
TSC (magnetometric Tester of Stress Concentration) type instruments and specialized scanning devices (SD) manufactured by Energodiagnostika Co. Ltd. are use to perform the inspection of boiler tubes.
Inspection is carried out on the left for repairs or reserve boiler. Special dressing is not required to carry out measurements of the magnetic leakage field intensity (Н) along the inspected heating surface tube generating lines, but the slag coverage has to be removed.
Two operators carry out inspection. One of them performs scanning with the sensor along the tube surface. Another operator records the measured Н values in the inspection results registration log.
One operator is allowed to carry out the inspection on condition of safety rules observance and in case the operator has the appropriate qualification and inspection experience.
Let us further consider some examples from the practice of the MMM method application during the diagnostics of boiler tubes and steam pipes.
At present thermal and atomic power stations face the problem of SCZs detection on steam pipe bends, being the sources of damages development.
Figure 1 shows the results of inspection by the MMM method of the extended bend zone ⌀219x19 mm, st.15Cr1MoV. Figure 1, a shows the scheme of the bend inspection and figure 1, b - the scanning device used for the inspection. Figure 1, c presents the magnetogram recorded during the inspection. The upper part of the magnetogram shows the bend's self-magnetic field distribution, and the bottom part - the distribution of this field's gradient.
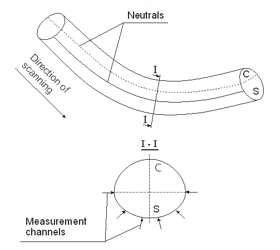
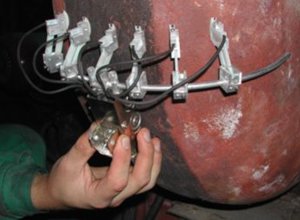
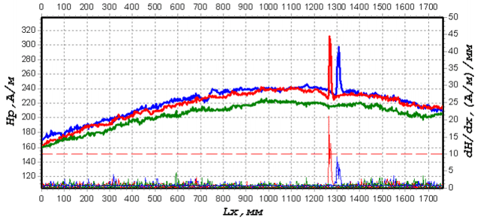
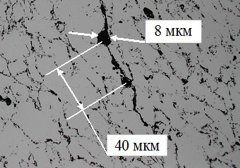
Figure 1. Results of inspection by the MMM method of the extended bend zone ⌀219x25 mm (st.15Cr1MoV) of a steam-circulating tube: а - scheme of the bend inspection; b - scanning device used for the inspection; c - distribution of the magnetic field Н and its gradient dН/dх along the extended bend generation line; d - metal structure recorded in the area of local variation of the magnetic field.
A "replica" for the metal structure analysis was taken from the bend surface in the area of abrupt local variation of the field and its gradient. Figure 1,d presents the metal structure recorded in the area of abrupt local variation of the magnetic field. In this case metal grinding to the depth of 100-150 micrometers was carried out to remove the damaged metal layer from the external surface. After removal of the damaged metal layer in the SCZ the bend was admitted for further operation.
Let us consider another example of the MMM method application. A problem of corrosion pits detection on internal heating surfaces of power boilers exists nowadays.
Figure 2, a shows the results of a heavy-duty power boiler ⌀60x6mm (st.12Cr1MoV) waterwall tube inspection. Figure 2, b shows the tube segment cut out from the SCZ detected by the MMM method. Corrosion pits were detected on the internal surface of the cutout tube segment.
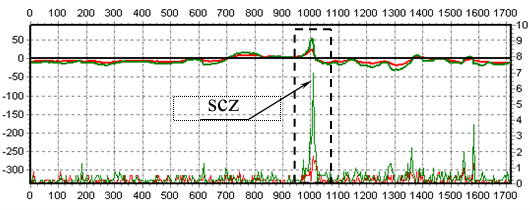
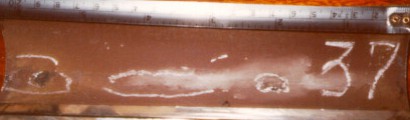
Figure 2. Results of the TGMP-206 boiler front waterwall ⌀60x6mm tube inspection.
It is known that gas-proof panels ensure furnace sealing against the cold air suction, increase the area of heating surfaces and thus improve boilers efficiency. However, from the very beginning of boilers operation with gas-proof panels their low maintainability was revealed. In addition, higher sensitivity of gas-proof panels to tube-to-tube thermal and hydraulic unbalancing and especially to local overheating of the metal was revealed in the course of operation. Even minor violations of "water-fuel" or "fuel-air" ratios allowed for conventional boilers can cause mass damaging of gas-proof panel tubes with their failure.
Figure 3 presents the fragment of the rear waterwall gas-proof panel tubes damaging in the form of their mass deflection in the area of field welded joints. Such type of damages was detected by Energodiagnostika Co. Ltd. experts in March 2004 on the gas-proof boiler 525 t/hr, st.No.4 at "Dora" TPS (Iraq).
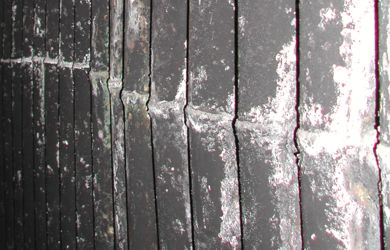
Similar damages are found on gas-proof boilers of electric power stations in Russia.
It is obvious that operation and repairs of boilers with gas-proof panels require higher qualification level of electric power station personnel performing maintenance of these boilers. It is also obvious that the gas-proof panels repair technique requires improvement and application of modern methods of technical diagnostics.
Investigation of gas-proof panels' stress-strain state (SSS) using the MMM method established that over 90% of all SCZs and damages developing in them are located near commercial, field and repair welded joints. Only in some cases SCZs and damages in them occur on tube segments located between welded joints. It was also established that metal damages are located mostly in welding heat-affected zones (HAZ), which are known to be process and structural stress concentrators. The established regularity of tube damages preferred location near welded joints is characteristic of gas-proof boilers, and it seems to be conditioned by their structural features and fundamentally different distribution of stresses and strains at thermal compensation as compared with waterwall tubes that have flexible attachment mounts in every 2 to 4 m along the furnace height. In case of insufficient self-compensation of an individual tube and/or several tubes within a gas-proof panel the distribution of associated stresses and strains occurring on each separate tube is conditioned by mutual impact of mass of tubes rigidly connected with each other inside the panel. And welding HAZ, being the weakest link by strength conditions, are the most susceptible to stresses due to lack self-compensation.
In confirmation of the above said, let us consider an example from the practice of the MMM method application during the diagnostics of gas-proof panels' SSS.
Figure 4 presents the results of individual tubes inspection in gas-proof panels on a boiler 525 t/hr, st.No.4 at "Dora" TPS (Iraq). It can be seen that abrupt increase of the magnetic field Н and its gradient dН/dх was recorded near field welded joints.
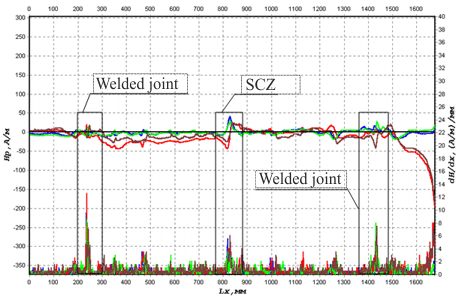
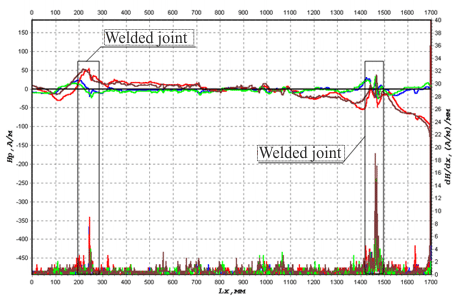
Figure 4. Inspection results of tube №26 (a) and tube №28 (b) of the front waterwall at the level of the upper bank of burners of boiler No. 4 of "Dora" TPS (Iraq).
The presented in figure 4 fragments of the magnetic field distribution are characteristic of individual tubes within the panels. By cutting out of specimens and the analysis of their condition, it was established that metal damages develop exactly on tube segments with the maximum value of the magnetic field gradient. The pattern of damages in SCZs located near the welded joints can differ depending on a number of operating factors. Based on the performed investigations of the metal’s state of specimens cut out from tube segments with SCZs, it was established that damages can develop both on the internal and on the external surfaces.
Damage in a SCZ develops mainly on the internal surface of a tube in case of low-quality boiler water and on the external surface in presence of corrosive components in furnace gases (for example, at burning of the low-quality fuel and the lack of air). As a rule, on internal tube surfaces damages develop in the form of separate pits or a pit chain (figure 2), and on external tube surfaces damages develop in the form of transverse scratches with frequency divisible by the tube wall thickness.
Papers [5, 6] consider the MMM method's capabilities for solution of various tasks of power boilers' heating surface tubes reliability assurance. In particular, the above mentioned papers [5, 6] consider the MMM method's capabilities for detection of segments with developing damages due to metal overheating, during inspection of welded joints in contact-welded parts and in points of coils welding to headers, at determination of intergranular corrosion on austenite tubes, at detection of jamming sites on tubes and in the support-suspension system of boilers causing the development of damages due to the lack of self-compensation of thermal expansion joints.
In conclusion it should be noted that till date at most of thermal power stations and in boiler-houses in Russia the mass tubes replacement remains the main measure for boiler tubes reliability assurance in case of their damaging. One of the reasons for such an approach to boilers safety and reliability assurance is the lack of efficient methods of early diagnostics of tube segments with developing damages. Based on the long-term experience (over 30 years) of the MMM method application at a number of power and hot-water boilers at electric power stations of Russia, Poland, China, Bulgaria, India and other countries, we can state the efficiency of the method in solution of the above mentioned problems.
References
1. V.T. Vlasov, A.A. Dubov. Physical bases of the metal magnetic memory method. Moscow: ZAO "TISSO", 2004. 424p.
2. G.V. Vstovsky, A.A. Dubov. Solution of the inverse problem of stress fields calculation on tube walls by magnetic leakage fields based on the non-linear model of the magnetoelastic effect // Zavodskaya Laboratoria, 2000, No.3.
3. V.G. Kuleev, A.A. Dubov, V.V. Lopatin. Zero lines of the normal leakage field on a defect-free tube surface at its elastic bending in any external magnetic field // Defectoscopia, 2002, No.1. pp. 13-26.
4. A.A. Dubov, Al.A. Dubov, S.М. Kolokolnikov. The metal magnetic memory method and inspection instruments. Training handbook. Moscow: ZAO "Tisso", 2008. 363 p.
5. A.A. Dubov. Boiler pipes diagnostics using the metal magnetic memory. Мoscow: Energoatomizdat, 1995. 112 p.
6. A.A. Dubov, Al.A. Dubov, S.М. Kolokolnikov. Technical diagnostics of steam and hot-water boiler heating surface tubes the metal magnetic memory: Guidance Manual of Public Administration Institute of Advanced Training, 2006. 110 p.