New requirements to methods and tools for diagnostics of materials' stress-strain state
Dr. A. Dubov
At present all leading diagnostic centers of the world are occupied with the problem of stress and strain control in working structures with the purpose of their state assessment. However it is known that the effectiveness of the inspection methods remains low when they are used in practice. Improvement of effectiveness of non-destructive testing (NDT) of technical objects' stress-strain state (SSS) during their lifetime assessment gains special significance.
At present a large arsenal of methods and means for non-destructive testing of residual stresses (RS) in engineering products and stress-strain state (SSS) control in operated industrial objects has been accumulated. However during their practical use a large number of scientific-technical problems occur and the lack of scientifically proven metrological base for certification and calibration of devices and instruments for products’ SSS characteristics measurement should be noted among them.
In particular, one of the most important metrological problems is that most of methods and means for SSS NDT are calibrated during the tensile testing of specimens focusing on conventional mechanical characteristics. Then the dependencies obtained in such a way are transferred to the real equipment without taking into account the scale factor, locality, time and speed of damages development.
Based on experimental and theoretical investigations of physical strains distribution patterns on standard specimens of various steels as well as on the accumulated experience of the metal magnetic memory development and practical application, the paper points out the discrepancy between the actual physical parameters of the internal stresses with the "usual" conventional mechanical properties of materials.
The presented in the paper results of investigations point to the necessity to develop new regulatory metrological documentation in the field of SSS NDT in order to eliminate the discrepancy revealed. The developed by the author in collaboration with TC-132 of Federal Agency for Technical Regulation and Metrology (Rosstandart) new national standards that establish general requirements to various methods and devices for SSS NDT are the first and the most significant step towards improvement of efficiency of equipment and structures' actual state assessment.
Many years of experimental and practical experience in development and practical application of the magnetic memory method for diagnostics of various objects revealed and proved objectiveness of the "discrepancy" of real values of internal stress physical parameters with "usual" limiting values of mechanical characteristics, for example, ultimate strength limit.
The results if theoretical investigations of physical strains distribution patterns [1] made it possible to explain the observed "discrepancies" and proved the incorrectness of the known assessment criterion of the material's true state in local zones of the developing damage by the degree of closeness to reference limiting mechanical characteristics of the material.
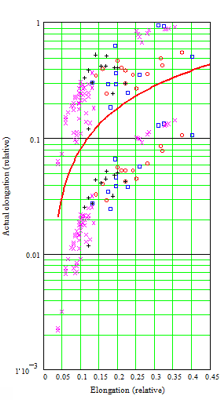
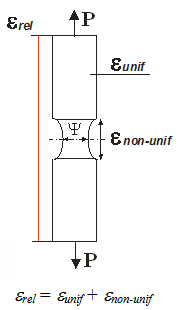
Figure 1. The ratio of relative elongation (ε rel) at fracture (solid curve) and actual values of average strain in areas of: non-uniform (ε non-unif - points above the curve) and uniform (ε unif - points below the curve) strain for various materials.
Investigations of strain and strength properties of 98 different steels and alloys showed steels (figure 1) that average values of specimens tensile strain in areas of non-uniform and uniform strain differ essentially (by several times) from the values of limiting mechanical strain characteristics of the material (ε rel). And local values of strains differ by orders already! It means that the limiting state criteria obtained during ordinary mechanical testing of specimens cannot reflect the limiting state of the material and, moreover, the limiting state of a structural element.
But in order to realize this it is necessary to overcome the ingrained notion of internal stresses and to remember that the stresses - "sigma", which we are all so used to, are not stresses. They are the internal specific force applied to a specimen of a specific shape and changing internal stresses - they are a conditional equivalent of internal stresses!
"Conditional" is because the prerequisites are: the specimen of a specific shape and a specific sequence of testing.
Figure 2 shows in sequential order how the external specific force, while "splitting" into components, affects the material deforming it in different directions (sliding, normal, latitudinal) and rotating it in space, thereby causing occurrence of corresponding internal forces of the material's resistance to strain, which finally determines the input of the material's self-energy for resistance to external load. It is obvious that the strains that can be measured (ε long - longitudinal and ε trans - transverse) represent algebraic sums of internal physical strain vectors projections to the directions usual for us - along and transverse the axis of the applied force.
It should be noted that the most terrible consequence of the deep-seated confusion in understanding of the nature of internal stresses, we may say insidious delusion, begins to emerge only now when there arose a vital problem of determination of the material's state and performance - an important component of the problem of complex engineering objects' residual lifetime assessment.
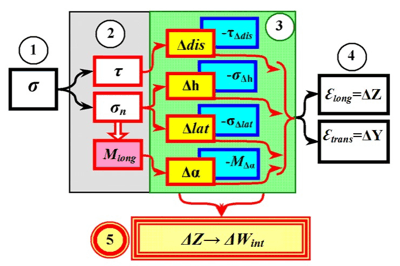
τ - shear stress;
σn - normal stress;
Mlong - torque;
ΔZ and ΔY - axes, along which the longitudinal εlong and transverse εtrans are measured, respectively;
Δdis and τΔdis - displacement (slip) strain and stress;
Δh and σΔh - normal strain and stress;
Δlat and σΔlat - latitudinal strain and stress;
Δα and MΔα - angular strain and torque;
ΔV - volume of structural element;
ΔWint - internal energy of resistance to strain.
There is a danger that the mechanical properties obtained during the specimens testing - reference limiting values of the specimens strain and specific forces - conditional equivalents of internal stresses - began to be considered the inherent characteristics of the material that determine its ability to resist any external loads regardless of the product's shape, in which this material is embodied. This was the source of the principal error common to all methods of internal stress "measurement" without any exception.
The results of experimental and theoretical investigations obtained in [1] allowed to "materialize" the conclusions, which facture mechanics practically came to grips with long ago, and to represent the limiting states and basic concepts closely related to them as follows:
- limiting state of the material - the minimum possible density of internal energy - the limiting potential determined solely by the average internal energy density, which is an individual quality of the material, and it does not depend on the size of structural elements, or its conditions of loading;
- limiting state of the structural element is determined by the size of the local area in which the material has reached the ultimate state, and the size of the structural element where this local area is located;
- the size of the local area is determined by individual characteristics of the material, the dimensions of the structural element and its loading conditions and, in turn, determine the nature of the local strain actual distribution in the volume of the structural element;
- the actual state of the material in the local area is the value of the actual internal energy density - the actual potential determined by individual characteristics of the material, the location of the investigated area in the structural element's volume, the element size and conditions of its loading;
- internal stresses - the difference of potentials - is the difference between the internal energy density in the local area and in the areas adjacent to it.
Moreover, now it can be said that internal stresses are a special unified energy characteristic of the material's equilibrium state, which is determined (see figure 2) by a number of physical strain-force parameters displaying a variety of options of internal energy variation at various variants of impact on the material embedded in a specific shape.
Any material has its own internal energy characterized by the average energy density that can be represented by two zero rank tensors - scalar and vector potentials. The energy distribution in the volume of even "isotropic" material is not homogeneous but is characterized by strict order of each of the possible and quite certain directions of the initial energy variation - three linear (normal) vectors (first rank tensor) and one axial (rotational) vector. These are all individual qualities or properties of the material determined by one characteristic - the average energy density that depends neither on the object's shape nor on the external impact nature. But at the same time "rather definite" linear directions of initial energy value variation - normal, shear and latitudinal, determined by the glide plane position in the force or other external field space, - depend already on the objects' shape, in which the investigated material is embedded.
Any external impact - from simple uniaxial to the most complex - on a specific object made of the investigated material, whether a specimen or a complex part, always "splits" in the material into three force and three torque (rotational) components (and only during uniaxial loading of a cylindrical specimen - into two force and one torque components).
During resistance to external impact the material uses its own energy. Its input can be evaluated by the work of the external field - strain-force parameters expressed by two full second-rank tensors (force and strain) or two pairs of linear (symmetrical) and rotational (antisymmetric) tensors. It should be noted that the loss of antisymmetric rotational tensor in the theory of materials' resistance led to deep misconception of "main stresses" and "main strain" existence. It is impossible neither theoretically (of course, unless a mistake is made), nor in real conditions to find such an “area without shear forces” and torques! It is easier to understand in physically: the material's energy consists of two practically equal in value components - potential (electrostatic) that determines "repulsion" of atoms and quantum that determines "attraction" of atoms. And it follows that during any impact on the material both fields - quantum (gravity) and potential (repulsive) always "work" in any of its areas. So, a pair of antisymmetric tensors lost by the theory of materials' resistance precisely describes the input of the quantum component of the materials' internal energy for resistance to external impact. And in general, what would remain of the material if we really ignore the forces drawing the atoms together?
As we can see, the well-known values of limiting states - yield strength and ultimate strength, obtained during ordinary mechanical testing of specimens, can not reflect the material's limiting state and, moreover, the limiting state of a structural element.
Thus, the analysis of investigation results prompts a conclusion known from the facture mechanics that we should already speak about several different failure criteria: the limiting value of normal strain during uniaxial tension, the limiting value of latitudinal strain during uniaxial compression and the limiting value of shear strain during torsion or bending as well as various combinations of limiting values during complex loading.
All this requires a more careful approach to the diagnostics of the material's stress-strain state and to the procedure of assessment of the extent of the actual material's state closeness in a local area of a structural element to the limiting value both for the material and for the entire structural element because its is clear now that this is far from being the same!
It is completely obvious that prediction of possible period of safe elements operation in real "ageing" structures (basic alternative of damages development) by the results of the material's SSS diagnostics using calibration curves, obtained during ordinary mechanical testing of specimens without evaluation of time and speed of fatigue damage development in a specific and in specific conditions, is not only useless but is extremely dangerous!
Moreover, considering the acute (from units to several tens of microns) locality of the fatigue damaging development process, peculiarities of local physical strains distribution and their correlation with the average strain values it can be stated that, using the conventional active methods of diagnostics with a large averaging base (10 mm at best), we, most probably, shall not simply detect the developing damage area, not to mention the possibility to determine the parameters of the developing damage.
The obtained results of physical strains distribution patterns investigation clearly indicate the necessity to develop the new regulatory documentation regulating certification of devices and instruments for diagnostics of structural materials' stress-strain state and, of course, of the techniques for calibration of devices and instruments for SSS diagnostics.
It should be noted here that the diagnostics of structural materials' SSS represents the next after flaw detection and higher level of diagnostics. It requires a new ideology, a new scientifically grounded methodology that would define goals and tasks of diagnostics as well as the assessment criteria of structural materials' actual stress-strain state.
The point is that the lack of general requirements to measured SSS characteristics and the lack of metrological base for certification and calibration of devices and instruments for materials' SSS characteristics measurement lead to ambiguity of initial requirements and erroneous methodological approach to the developed devices and instruments. It causes not only unacceptably low reliability of measurement results (although, as was shown earlier, in this context it cannot be spoken about at all) but also very often makes it impossible to identify correctly the measured parameter of the physical field used and of the measured physical characteristic of the investigated material.
GOST R 52330-2005 "Non-destructive testing. Stressed-strained state test on industrial objects and transport. General requirements" put into effect in 2005 is the first and important step in making methods and means of structural materials' SSS diagnostics an efficient and truly necessary and useful tool for actual state assessment of structural materials' and structures' as such.
One of the main general requirements to all SSS NDT methods and means in the above mentioned national standard is the necessity to detect maximum stress concentration zones (SCZs) - the sources of damages development - in structural elements. SCZs are not only the areas known in advance where the structural features create various conditions for distribution of stresses due to the external working load. But these are also the randomly located areas with large local strains occurred due to initial inhomogeneity of the metal in combination with off-design additional working loads.
The new standard GOST R 53006-2008 "Engineering diagnostics. Lifetime assessment of potentially dangerous objects based on the quick methods. General requirements" was approved and put into effect in November 2008 by the order of the Federal Agency for Regulation and Metrology of RF No.309-st. dated 13.11.2008.
Passive NDT methods, which use the internal energy of the structures' metal, are referred to quick methods, namely:
- the method of acoustic emission (AE);
- the metal magnetic memory (MMM) method;
- thermal inspection.
At present these methods are most widespread in practice for the purposes of early diagnostics of damages in metal components and structures. The principal distinctive feature of such an approach to assessment of the lifetime is execution of a 100% inspection of the IO with detection of all potentially dangerous stress concentration zones (SCZs), which are the sources of damages occurrence in the course of further operation of metal components.
The new National Standard GOST R 53006-2008 also reflects the following basic provisions:
- it is suggested to use the actual energy characteristics, which can be determined using the MMM, AE and thermal methods, as basic criteria of the limiting state of the metal;
- the block diagram of the residual lifetime determination was corrected with the emphasis on the modern quick methods of engineering diagnostics;
- it is suggested to carry out calibration strength calculations with residual lifetime assessment for SCZs being in operation, taking into account the actual structural-mechanical properties of the metal, detected during the inspection;
- recommendations of the National Standard GOST R 52330-2005 were taken into account.
In 2010 the Federal Agency for Technical Regulation and Metrology (Rosstandart) approved two new national standards [2, 3] specifying general requirements to classification and procedure of SSS NDT methods selection.
In conclusion it should be noted that in contrast to the regulatory-metrological problems, being the objective problems, for which the methods of solution is clear and described in this paper, the psychological problems, which SSS NDT experts have to overcome, have already gained the subjective and widespread nature. The quicker the wide range of experts overcomes these psychological problems in perception of the new requirements to SSS NDT methods and means, the quicker we shall get closer to the objective assessment of equipment and structures’ lifetime.
References
1. Vlasov V.T., Dubov A.A. Physical theory of the "Strain-failure" process. M.: ZAO "TISSO", 2007. 517 p.
2. GOST R 53966-2010. Non-destructive testing. Stress-strain state control of the material in structures. General requirements to methods selection procedure.
3. GOST R 53965-2010. Non-destructive testing. Determination of mechanical stresses. General requirements to methods classification.