Capabilities of the metal magnetic memory method for monitoring of cracks development
A.A. Dubov, Al.A. Dubov
Article [1] presented the capabilities of the metal magnetic memory (MMM) method for studying the strain-failure process of steel specimens under cyclic loading. Fatigue curves, plotted by variation of the specimens' self-magnetic field during cyclic loading, experimentally confirmed the possibility to assess the equipment lifetime by the metal magnetic memory parameters.
Magnetograms, recorded in the real time mode in the course of specimens cyclic loading, confirmed the possibility of using the MMM method and the TSC instruments for monitoring the technical condition of equipment under load directly during its operation (Figure 1).
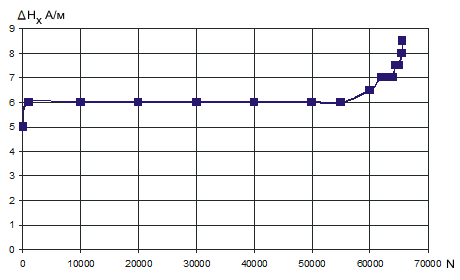
Let us further consider the capabilities of the MMM method for monitoring cracks development under load in conditions of operated "cocoa press" installed at OJSC "Babaevsky Confectionery Concern".
In 2010, during the "cocoa press" housing inspection in the fillet area using the MMM method, a crack with the length of more than 100 mm was detected (Figure 2). Additional ultrasonic testing showed that the maximum crack depth was 70 mm at the housing thickness of 130 mm. The enterprise management took the decision to temporarily continue operating the press. In order to monitor the crack development during operation in the maximum stress concentration zone, the TSC (Tester of Stress Concentration) type recording instrument sensors were installed near the crack). Figure 3 shows the location of the sensors installation near the crack.
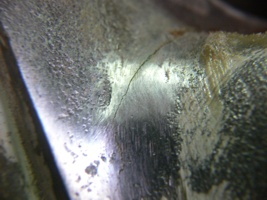

Figure 4 shows the graph of hydraulic oil pressure time variation per the press piston. Points 1, 2, 3, 4 in Figure 4 – are oil pressure variation reference points. One piston load cycle time is 28 minutes.
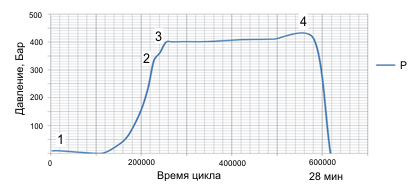
Figure 5 presents the magnetograms of the self-magnetic field H variation, recorded using the TSC instrument sensors installed near the crack in three load cycles I, II, III.
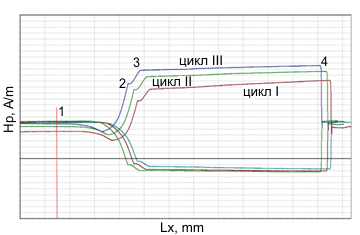
By time and piston load the reference points 1, 2, 3, 4 in the magnetograms correspond to points 1, 2, 3, 4, indicated in Figure 1.
Comparison of Figure 4 and Figure 5 shows that the graphs of the magnetic field H variation near the crack and variation of oil pressure on the piston qualitatively coincide. It is also can be seen in Figure 5 that the H field increases slightly with each load cycle. As a result of such measurements, it was found that after 6÷7 load cycles, the H field value stabilized. And it was noted that each minor increase in the crack development of is accompanied by a step in the magnetic field variation, recorded by the TSC instrument sensors.
Reference
1. N.A. Makhutov, A.A. Dubov, A.S. Denisov. Study of statistic and cyclic strains using the metal magnetic memory method // Zavodskaya laboratoriya, 2008, No.3. pp. 42-46.