The Metal Magnetic Memory Method - a New Trend in Engineering Diagnostics
Traditional methods and means of diagnostics (ultrasonic inspection, magnetic particle inspection, X-ray) are oriented to detecting the already developed defects and by their designation can not prevent sudden fatigue damages of equipment, which are the main reasons of failures and sources of maintenance staff traumatism.
It is known that stress concentration (SC) zones, in which corrosion, fatigue and creep processes develop most intensively, are the main sources of damages occurrence in operating structures. Consequently, detecting SC zones is one of the most important tasks of equipment and structures diagnostics.
Variations of metal properties (corrosion, fatigue, creep) in SC zones are the processes preceding operating damaging. Metal magnetization, reflecting the actual stress-strained state of pipelines, equipment and structures, changes accordingly.
At present a principally new method of equipment and structures diagnostics based on using of metal magnetic memory has been developed and implemented successfully in practice. The MMM method unites the potential opportunities of non-destructive testing (NDT) and fracture mechanics due to which it has a number of significant advantages over other methods at inspection of industrial objects.
Basic practical advantages of the new diagnostics method as compared to the known magnetic and other traditional methods of non-destructive testing (NDT) are:
- application of the method does not require special magnetizing devices as the phenomenon of equipment and structures units magnetization in the process of their operation is used;
- locations of stress concentration due to working loads, which are unknown beforehand, are determined in the course of their inspection;
- metal dressing or any other preparation of the test surface is not required;
- small-sized instruments, self-contained power supply, recording systems and a memory unit up to 32 Mb are used to perform inspection by the proposed method;
- special scanning devices allow testing of pipelines, vessels and equipment in the express-control mode at a speed of 100 m/h and more.
The MMM method is the most suitable practical NDT method at assessment of actual stress-strained state. Therefore application of the new diagnostics method is the most effective for equipment units life assessment.
The suggested diagnostic method, based on application of metal magnetic memory, allows performing an integral evaluation of a unit state considering the metal quality, actual operating conditions and its structural features.
The main task of the MMM method is detecting on the test object of the most dangerous sections and units characterized by SC zones. Then, using, for example, UT in SC zones, the presence of a specific defect is detected. Based on calibration strength calculations of the most stressed units, detected by the MMM method, the equipment actual life assessment is carried out.
Besides that, MMM and the appropriate inspection devices allow:
- carrying out early diagnostics of fatigue damages and predicting equipment reliability;
- documenting inspection results and making the equipment state data bank;
- performing express grading of new and old parts by their susceptibility to damaging;
- detecting the future crack location and propagation direction on the test object with accuracy up to 1 mm as well as recording of the already formed cracks;
- inspecting in some cases of pipelines and vessels without insulation removal.
What is principally new in the suggested inspection method?
From the analysis of known magnetic methods the following obligatory conditions of their application are arise. Firstly, the magnetizing devices should be necessarily used, and secondly, the known magnetic methods can be applied effectively only on condition that locations of stress concentration and defects in the control object are known in advance. Besides, the known magnetic inspection methods require, as a rule, metal dressing and other preparatory operations. It is obvious that application of conventional magnetic inspection methods in extended structures and on equipment at such conditions is practically impossible. For example, the task of specially magnetizing the tube system, whose length on a modern power boiler approaches 500 km, is unreal. It is impossible to know in advance stress concentration zones (the main sources of damages development) on each boiler tube due to different process, design and operating factors influencing their formation.
It is known at the same time that most of metal structures and equipment of ferromagnetic materials is susceptible to "self-magnetization" in the magnetic field of the Earth under influence of working loads.
The figure shows the scheme of magneto-elastic effect action (ΔBr - residual inductions change; Δσ - cyclic loads change; Нe - external magnetic field). If a cyclic load σ acts in some area of a structure and an external field is present (for example, the magnetic field of the Earth), the residual induction and residual magnetization growth occurs in this area.
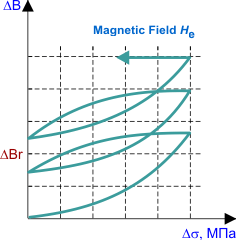
The phenomenon of equipment and structures "self-magnetization" is fought against everywhere (shipbuilding, power engineering, ball bearing and other industries). Upon studying this magnetization phenomenon on the example of boiler tubes, it was suggested for the first time to use it for the purposes of engineering diagnostics. At equipment and structures "self-magnetization" various magnetostriction effects appear. However, the new inspection method uses an aftereffect (in all varieties of magnetostriction effects), which becomes apparent as the metal magnetic memory to actual strains and structural changes in equipment metal. The more detailed information on the principal differences of the MMM method from other known magnetic NDT methods can be found in a A. A. Dubov "Fundamental difference of the metal magnetic memory method from other known magnetic non-destructive testing methods. Totals and prospects of the method development".
Metal magnetic memory is an aftereffect, which becomes apparent in the form of residual magnetization of products and welded joints metal formed in the course of their fabrication and cooling in a weak magnetic field or in the form of irreversible changing of products magnetization in stress concentration and damaging zones due to working loads.
Note: A weak magnetic field is a geomagnetic field and other low-intensity external fields. The more clear boundary between weak and strong magnetic fields is considered in the book "The Physical Bases of the Metal Magnetic Memory Method" by Vlasov V.T., Dubov A.A. M.: ZAO "TISSO", 2004.
The metal magnetic memory method is a non-destructive testing method based on registration and analysis of self-magnetic leakage fields (SMLF) distribution on products surface for determination of stress concentration zones, defects, metal and welded joints structure inhomogeneity.
The self-magnetic leakage field of a product is a magnetic leakage field occurring on the product surface in the zones of dislocations stable slipbands under the influence of operational or residual stresses or in zones of maximum inhomogeneity of metal structure in new products.
For individual items, products and welded joints MMM is based on registration of own leakage magnetic fields occurring in residual stress concentration zones after their fabrication and cooling in the magnetic field of the Earth. During fabrication of any ferromagnetic products (fusion, forging, heat and mechanical treatment) the mechanism of real magnetic texture formation takes place simultaneously with solidification at cooling, as a rule, in the magnetic field of the Earth. In areas of the maximum lattice defects concentration (for example, dislocation clusters) and structural inhomogeneities domain boundaries occur with exit to the product surface in the form of SMLF normal component sign alternation lines. These lines correspond to the part section with the maximum magnetic resistance and characterize the maximum metal structure inhomogeneity zone and, accordingly, the internal stresses maximum concentration zone (SCZs).
Currently more than 60 guidance documents and inspection techniques has been developed and practically applied in power engineering, chemical, petrochemical, oil- and gas-refining, oil, gas and other Russian industries. The complex of researches for theoretical substantiation of the method is conducted jointly with a number of Russian institutes. The quantitative and qualitative criteria allowing performing early diagnostics of equipment fatigue damages and life assessment using the MMM method are developed.
During the period from 1990 to 2019 the experts of Energodiagnostika Co. Ltd carried out industrial researches with a state assessment of more than 320 steam and hot-water boilers, more than 245 steam and gas turbines, more than 220 vessels and apparatuses, more than 3000 km of various process purpose pipelines; the quality inspection of machine-building products at more than 50 plants and companies both in Russia and other countries is carried out; experimental control of a rails and wheel sets on railway transport enterprises, bridge structures, hoisting mechanisms and other technical objects is performed.
The MMM method is applied at more than 1000 enterprises of Russia. Besides Russia, the method was implemented at a number of enterprises of 44 countries: Angola, Argentina, Australia, Azerbaijan, Bahrain, Belarus, Bosnia and Herzegovina, Brazil, Bulgaria, Canada, China, Colombia, Croatia, Czech Republic, Finland, Germany, Hungary, India, Iran, Iraq, Israel, Italy, Japan, Kazakhstan, Korea, Latvia, Lithuania, Macedonia, Malaysia, Moldova, Mongolia, Montenegro, the Netherlands, Oman, Poland, Romania, Serbia, South Africa, Switzerland, Tajikistan, Turkmenistan, UAE, Ukraine, the USA.
The following Russian standards were prepared and put into effect:
- GOST R ISO 24497-1-2009. Non-destructive testing. Metal magnetic memory method. Part 1. Terms and definitions.
- GOST R ISO 24497-2-2009. Non-destructive testing. Metal magnetic memory method. Part 2. General requirements.
- GOST R ISO 24497-3-2009. Non-destructive testing. Metal magnetic memory method. Part 3. Inspection of welded joints.
- GOST R 52330-2005. Non-destructive testing. Evaluation of deformations in industrial and vehicle structures. General requirements.
- GOST R 53006-2008. Estimation of potential dangerous objects lifetime on the basis of express methods. General requirements.
- GOST R 55044-2012. Technical diagnostics. The order of selection of test objects when calibrating diagnostic tools for the stress-strain state of structural materials. General requirements.
- GOST R 56663-2015. Non-destructive testing. Quality control of engineering products by the residual magnetization that has developed during their manufacture. General requirements.
During the period from 1994 till 2019 50 IIW documents with positive resolutions on the metal magnetic memory method were issued.
The International Standard ISO 24497-1:2007(E), 24497-2:2007(E), 24497-3:2007(E) on the metal magnetic memory method is approved in 2007 as a result of positive voting among 18 IIW member countries and more than 10 ISO Committee countries.
Currently, based on international standards by the MMM method, national standards have been put into effect in Bulgaria, Canada, China, Iran, Italy, Korea, Mongolia, Poland, Russia, Ukraine.
Significant experience of industrial and laboratory investigations, availability of techniques, guidance documents, scientific and technical reports allowed developing the normative-technical documentation (NTD) on certification of the metal magnetic memory method, inspection devices and personnel. Besides the techniques and GD, the normative-technical documentation includes: the requirements to technical knowledge of the experts studying the MMM method; the program of Level I, II and III experts training (approved by the State Engineering Supervision (Rostechnadzor) of Russia); passports and technical specifications to inspection instruments; operating manuals, techniques for inspection instruments calibration and testing; the users manual to the software for computer processing of results; training handbook.
Articles on the metal magnetic memory method:
- A.A. Dubov. The metal magnetic memory method
- A.A. Dubov. Purpose and practical capabilities of the metal magnetic memory method
- A.A. Dubov. Metrological aspects in the metal magnetic memory method
- A.A. Dubov. Fundamental difference of the metal magnetic memory method from other known magnetic non-destructive testing methods. Totals and prospects of the method development
- A.A. Dubov. The totals of application of the metal magnetic memory method to industry in Russia and other countries
- A.A. Dubov, V.T. Vlasov. On the problem of stress-strain state characteristics measurement of structural materials on complex engineering objects. Energy concept of materials stress-strained state (SSS) diagnostics
- A.A. Dubov, Al.A. Dubov. Problems of oil and gas pipelines' stress-strain state control and their solution using the metal magnetic memory
- A.A. Dubov. Stress-strain state control of gas pipelines during assessment of their lifetime
- A.A. Dubov. Process pipelines inspection without insulation removal using scanning devices and the metal magnetic memory method
- A.A. Dubov, Al.A. Dubov. Non-contact magnetometric diagnostics of pipelines and perspectives of its development
- A.A. Dubov. Technical diagnostics and monitoring the condition of equipment and structures at the present stage of development
- A.A. Dubov. Problems of ageing equipment residual life assessment
- A.A. Dubov. Assessment of equipment lifetime using the metal magnetic memory method
- A.A. Dubov. Metal magnetic memory method and its capabilities for diagnostics of power boiler elements
- A.A. Dubov. Detection of local stress concentration zones in engineering products - the lacking link in the non-destructive testing system
- V.M. Matunin, A.A. Dubov, Al.A. Dubov. Determination of metal's mechanical properties by hardness parameters in stress concentration zones detected in engineering products using the metal magnetic memory method
- N.A. Makhutov, A.A. Dubov, A.S. Denisov. Study of static and cyclic strains using the metal magnetic memory method
- A.A. Dubov, N.A. Semashko, V.Yu. Privalov, L.R. Botvina, A.B. Tsepelev. On relationship of magnetic, acoustic and mechanical characteristics assessed during tensile testing of steel specimens
- A.A. Dubov, Al.A. Dubov. Capabilities of the metal magnetic memory method for monitoring of cracks development
- A.A. Dubov, S.M. Kolokolnikov. Review of welding problems and allied processes and their solving using metal magnetic memory effect
- A.A. Dubov, Al.A. Dubov, A.A. Sobranin. Diagnostics of oil-production drilling rig units and components using the metal magnetic memory method
- A.A. Dubov. Reliability assurance of oil production facilities electric submersible centrifugal pump parts using the metal magnetic memory
- A.A. Dubov. Quality control of cast valves using the metal magnetic memory
- A.A. Dubov, S.M. Kolokolnikov, A.G. Medvedev, D.S. Boriskin. Integrated testing of liquid ammonia refrigerator tank welded joints
- A.A. Dubov. New requirements to methods and tools for diagnostics of materials stress-strain state
Basic publications:
1. Dubov A.A., Dubov Al.A., Kolokolnikov S.M. Method of metal magnetic memory and inspection instruments. Training handbook. Moscow: Publishing House "Spektr", 2012.
2. Vlasov V.T., Dubov A.A. Physical theory of the "strain-failure" process. Part I. Physical criteria of metals limiting states. Moscow: Publishing House "Spektr", 2013. 488 p.
3. Vlasov V.T., Dubov A.A. Physical theory of the "strain-failure" process. Part II. Process thermodynamics. Moscow: Publishing House "Spektr", 2016. 223 p.
4. Vlasov V.T., Dubov A.A. Physical bases of the metal magnetic memory method - 2-nd ed. Moscow: Publishing House "Spektr", 2019. 394 p.
5. Dubov A.A. Metal magnetic memory method. History of origin and development. Moscow: FSUE "Izvestiya" Publishing House, 2011.
6. Dubov A.A. I.C. 2029263. Patent of Russia and the C.I.S. countries. Method for residual stresses determination in products made of ferromagnetic materials. List of Inventions, No.5, 1995.
7. Proceedings of the First, the Second, the Third, the Fourth, the Fifth, the Sixth, the Seventh and the Eighth International Scientific-Technical Conferences "Equipment and structures diagnostics using the metal magnetic memory". Papers and summary to papers. Moscow: Energodiagnostika Co. Ltd, 1999, 2001, 2003, 2007, 2009, 2011, 2013, 2015.
8. Dubov A.A. Diagnostics of boiler tubes using the metal magnetic memory. Moscow: Energoatomizdat, 1995.
9. Dubov A.A. Diagnostics of turbine equipment using the metal magnetic memory. Moscow: ZAO "TISSO", 2009.
10. Dubov A.A. Diagnostics of pipelines, equipment and structures using the metal magnetic memory. Collection of papers and reports. Moscow: Energodiagnostika Co. Ltd, 2001.
11. Dubov A.A. Investigation of metal properties using the magnetic memory method // Physical metallurgy and thermal treatment of metals, No.9, 1997.
12. Dubov A.A. Express method of welding stresses inspection // Welding fabrication, No.11, 1996.
13. Dubov A.A. Diagnostics of rails fatigue damaging using the metal magnetic memory // In the world of NDT, No.5, 1999.
14. Goritzky V.M., Dubov A.A., Demin E.A. Investigation of steel samples structural damaging using the metal magnetic memory method // Testing. Diagnostics, No.7, 2000.
15. Dubov A.A. The problems of the ageing equipment life assessment // Labour safety in industry, No.12, 2002, pp.30-38.
16. Dubov A.A. The method of metal limiting state determining and equipment life assessment by magnetic diagnostic parameters // Testing. Diagnostics, No.5, 2003.