Inspection of wires and ropes
Inspection of wire
The presented below inspection technology can cover all types of welding and spring wires.
To ensure installation, repairs and operation of parts installed in gas- and oil-production boreholes the ⌀2,0 and ⌀2,6 steel wire is used. The wire is made of steel 40-70 according to GOST 9389-75, GOST 1050-88, GOST 14959-79 and GOST 1435-90.
In the course of operation and repairs the wire damages occur, which causes the large material loss. In order to prevent the occurrence of wire damages it is necessary to develop and implement non-destructive testing methods, allowing timely detection of stress concentration zones (SCZs). SCZs, being the sources of damages development, may occur both on the new and used wire.
Based on the analysis of the results of experimental investigations, carried out by Energodiagnostika Co. Ltd. experts on the ⌀2,0 and ⌀2,6 wire using the metal magnetic memory method, the following conclusions were made:
- The possibility to use the MMM method for quality inspection of both the new and the used wire was revealed.
- Inspection may be carried out at the production plant during the wire rewinding from one spool to another and directly at the boring plant during pulling-out or lowering-in of the equipment.
- The quantitative criteria of the metal's limiting state of the various-type wire were determined. These criteria need to be specified in the course of the industrial implementation of the MMM method and the appropriate instruments.
- It was established that the MMM method and the instruments of the TSC-4M-16 type allow detecting SCZs and zones of developing damages on the wire surface with the accuracy of up to 1 mm.
The main task of the MMM method consists in detection of SCZs, which are the zones of the anomalous distribution of the magnetic leakage fields on the surface of the inspected wire. Then, using the specialized "MMM-System" program, the wire grading is carried out by the degree of its susceptibility to damaging in SCZs. Screening and grading of the wire may be carried out directly during the inspection by the values of Kin, corresponding to the wire metal's limiting state before the formation of cracks. The value of Kin, corresponding to the metal’s limiting state, is determined in the course of experimental investigations separately for each dimension-type of the wire.
The inspection of the wire may be carried out both in the steady-state (at the plant) and in the field conditions near the boreholes.
In the steady-state mode the inspection is carried out during the wire rewinding from one spool to another. Fig.1 shows the inspection scheme.
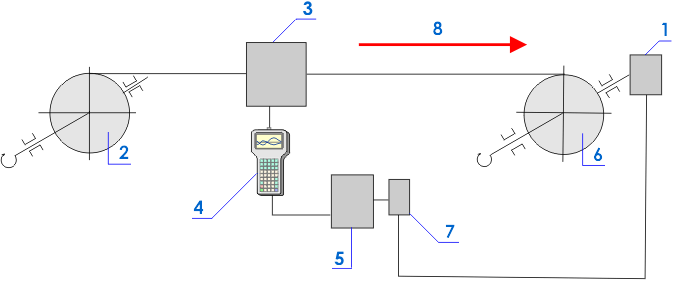
The drive motor 1 rotates the winding spool 6 at a constant specified rotating speed. The wire moves inside the guiding device combined with the measuring sensor 3. During the motor rotation and, accordingly, the wire rewinding from the spool 2 to the spool 6 the magnetic field Hp (A/m), measured with the sensors, is displayed in the form of graphs (magnetograms) on the screen of the instrument 4. The spool 2 rotates due to rewinding of the wire to the spool 6. The inspection may be carried out by one or two operators. In case an abrupt local variation of the Hp field or its gradient (dHp/dx) greater than the limiting value (specified in the technique) is displayed on the instrument’s screen, the operator stops the wire-feeding drive motor using the control panel 7 and marks the stress concentration zones with paint or a soft-tip pen.
The inspection according to the scheme shown in fig.1 may be performed in the automatic mode. In this case the entire wire length (up to 15 km, and the length may be even greater when the instruments' memory volume is enlarged) may be rewound from the spool 2 to the spool 6 at a speed of 1,2-1,8 km per hour. At the same time the diagnostic parameters Hp and dHp/dx are simultaneously stored to ROM of the TSC-4M-16 type instrument.
Fig.2 presents the photograph of a specialized Type 13 scanning device for the wire inspection.
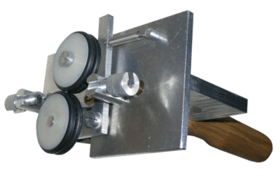
Fig.3 shows the fragment of the inspection results of a new ⌀2,6 mm (GOST 14959-79) wire.
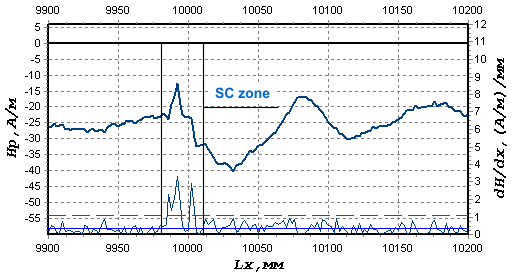
Inspection of steel ropes
The inspection of steel ropes is carried out using the Type 15 specialized scanning device, which covers the rope along the entire perimeter. The high effectiveness of the MMM method at inspection of both individual winds and the entire rope section was revealed.
Fig.4 shows the results of the ⌀16 mm rope metal inspection after the operating time of ~6700 load cycles on the mine equipment.
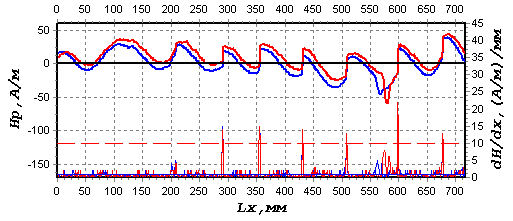