Express method of vessels and apparatuses inspection
Fig.1 shows the scheme of inspection. The operator moves the trolley-type scanning device along the welded joints and along the vessel generatrices in accordance with the technique. The multi-channel scanning devices (Type 6) are used for the simultaneous assessment of the vessel shell metal’s state in the zones adjacent to the weld.
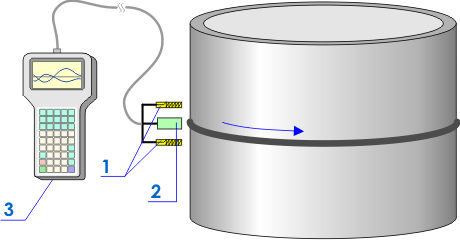
Fig.2 presents the inspection results of the PVC polymerization reactor girth weld. The local variation of the Hp field corresponds to the stress concentration zones and welding defects.
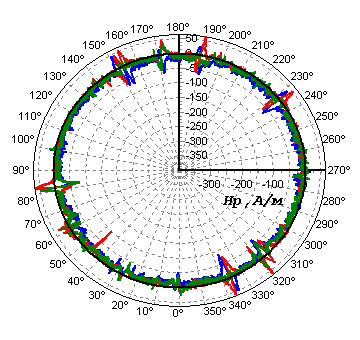
Fig.3, a shows the fragment based on the inspection results of a welded joint segment in a satisfactory state, and fig.3, b - the fragment of a cracked segment.
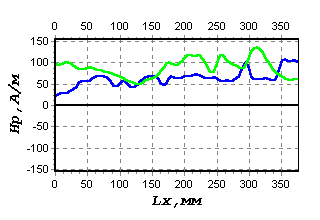
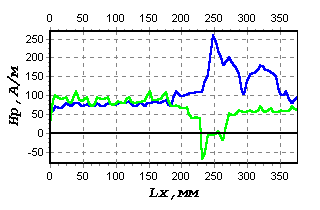
Fig.4 shows the arrangement of the stress concentration lines (SC lines) detected during the inspection by the metal magnetic memory method. In this case the SC lines formation resulted from the loss of the vessel stability. As a rule, the corrosion-fatigue wear of the metal occurs along the SC line on the internal surface of the vessel. A crack of the fatigue (or corrosion-fatigue) nature may occur on the external surface along the SC line.
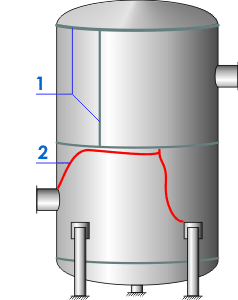
Fig.5 shows the example of butt-welded joints inspection on the ammonia converter casing (feed water heater) at "Nevinnomyssky Azot" JSC. The converter wall thickness was 200 mm, the diameter was 1550 mm. Inspection was carried out in the in-service state (P=240 atm., T=330°С). Fig.5, a shows the cracks arrangement on the welded butt joint W12 Local P.W.H.T., fig.5, b indicates the good quality of the welded butt joint W12, and fig.5, c characterizes the unsatisfactory quality of the welded butt joint W12 Local P.W.H.T. with the zones of transverse cracks formation (9-12 hours) and individual SC zones with developing damages at the depth of 200 mm.
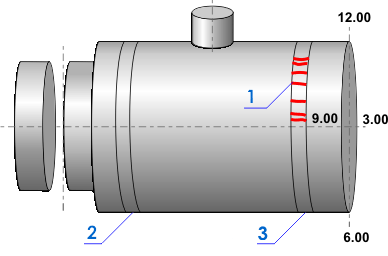
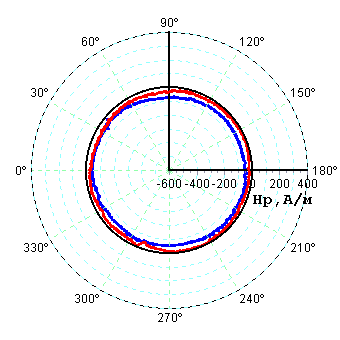
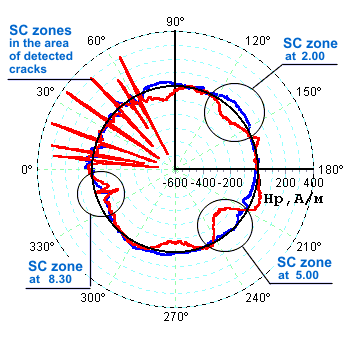
In January 1996 The Russian State Technical Supervision Body (Gosgortechnadzor) approved the "Technique for express inspection of vessels and apparatuses using the metal magnetic memory method".
This technique may be applied in power engineering, chemical, oil and gas refining, petrochemical, oil and gas industries during the inspection of vessels made of the ferromagnetic and paramagnetic (austenite) material. The technique and the corresponding instruments allow carrying out the inspection of the vessel's stress-strain state (under load and after its relief) simultaneously with flaw detection of welds. The technique also allows performing the inspection of fillet welds, which cause the problem for conventional NDT methods.
Based on the primary 100% inspection of the vessel using the MMM method, there is a possibility of inspection in future of the most stressed and susceptible to damaging zones only. The acoustic emission method based in-service control sensors can be installed in these zones with the accuracy of up to 1 mm.
It is feasible to carry out the vessel shell strengthening in the SC zones, detected by the MMM method, without waiting for the damaging development.