Diagnostics of heating surface tubes of steam and hot-water boilers
Inspection is carried out on the boiler shut down for the repairs. Fig.1 shows the scheme of the waterwall tubes inspection using a specialized magnetometric instrument - the TSC-type tester of stress concentration.
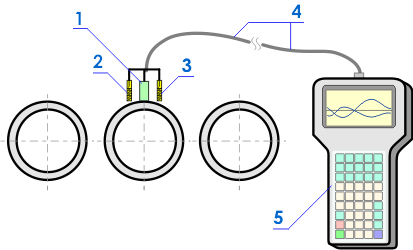
Fig.2, a shows the fragment of the inspection results in a SC zone on the waterwall tube of the boiler furnace gasproof panel. Fig.2, b shows the characteristic damaging of the gasproof panel waterwall tube.
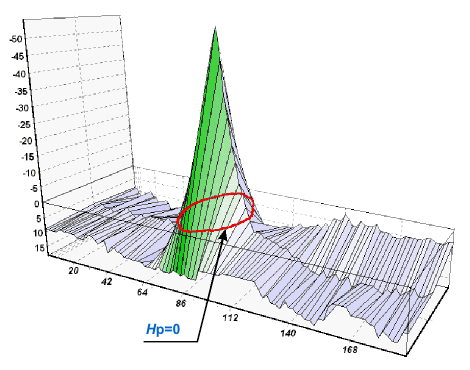
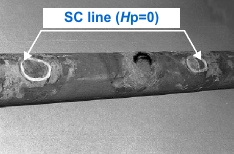
Fig.3 shows the fragment of the corrosion pit detection by the character of the residual magnetization field Hp distribution along the fire generatrix of the tube.
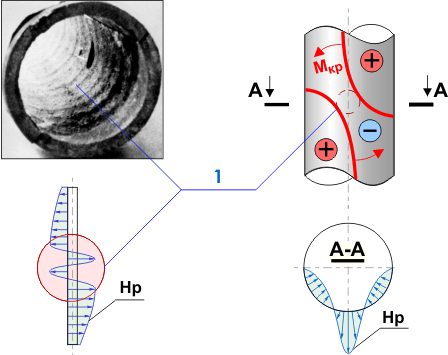
Fig.4 presents the example of the distribution of the normal (Hpy) and the tangential (Hpx) components of the self-magnetic leakage field (SMLF) recorded along the external generatrix of the boiler tube operating in conditions of the lack of self-compensation.
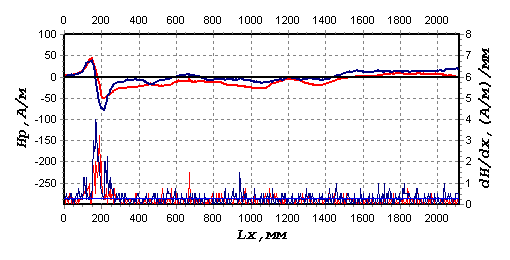
The suggested method of diagnostics allows carrying out the mass inspection of welded butt joints on HS tubes and in the units of tubes and coils attachment to collectors without metal dressing. The method may be applied effectively for detection of SC zones on superheater tubes made of pearlitic and austenite steel grades. Based on the results of the inspection using the metal magnetic memory method, it is possible to perform cutting out of representative tube specimens for the analysis of the metal's state, determination of the amount and the quality of internal deposits. The method allows carrying out simultaneously flaw detection and diagnostics with revealing of the reasons of SC zones and damages occurrence.
There is an experience of the MMM method application for early diagnostics of gasproof panel tubes damages and improvement of the effectiveness of their repairs. It is suggested, using the results if the inspection by the MMM method, to remove the reasons of SC zones occurrence during the boilers repairs by means of ensuring the self-compensation of tubes. Performing the metal's external surface grinding in SC zones is also an effective measure.
The developed diagnostic method belongs to quick methods and allows inspecting all the tubes of the high-power boiler furnace chamber within 5-6 working days.
The "Methodic Guideline for engineering diagnostics of steam and hot-water boiler heating surface tubes using the magnetic memory of metal" (GD 34.17.446-97) was approved by "Russian UES" RJSC and agreed with the Russian State Technical Supervision Body (Gosgortechnadzor). This guidance document is mandatory for application at the electric power engineering industry enterprises and may be applied at the enterprises of other industries, owning the boilers, which are subject to supervision of the Russian State Technical Supervision Body. In 2002 this guidance document was supplemented and revised taking into account the accumulated experience.