Diagnostics of steam turbine blades
Inspection is carried out on the convex surface of the blade on the side of steam inlet and outlet. Fig.1 shows the scheme of the blades inspection.
Scanning with the TSC-type instrument sensor is performed in the direction from the blade root section to the peripheral section or conversely.
It is recommended to execute all the blades inspection operations step-by-step for the blades of a specific stage.
In the course of the inspection the TSC-type instrument's screen displays the graphs of the Hp leakage field distribution along the blade length. The inspection results are stored to the instrument's ROM for their further processing on the IBM-compatible computer.
The blades operating in the most stressed conditions are determined based on the inspection results. These are the blades with the stress and strain concentration lines (SC lines) located transverse to the blade wing and having the maximum Hp field gradient: Kin=dHp/dx. The value of the filed gradient Kin, characterizing the level of residual stresses in the blade, is determined automatically and displayed on the screen by the operator's command. The technique for blades inspection, submitted to the Customer, specifies the limiting values of the field gradient, which precede the crack formation.
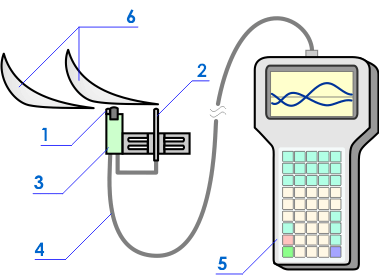
Fig.2 shows the results of blades #31, 32 and 33 inspection of stage #33 of the K-300-240 steam turbine low-pressure rotor (LPR) at Konakovo TPS using the metal magnetic memory method. The distribution of the Hp field and, accordingly, of the field gradient (dHp/dx) recorded on the blade #31 (see fig.2, a) characterizes its satisfactory state. It is seen in figures 2, b and 2, c that the abrupt variation of the Hp field and, accordingly, of the field gradient Kin was recorded on the blades #32 and #33 at the distance of 180-200 mm from the root. Based on the available experience, such Kin values are close to limiting values. It should be noted that the numerical values of Kin also depend to some extent on the sensitivity of the inspection instruments used.
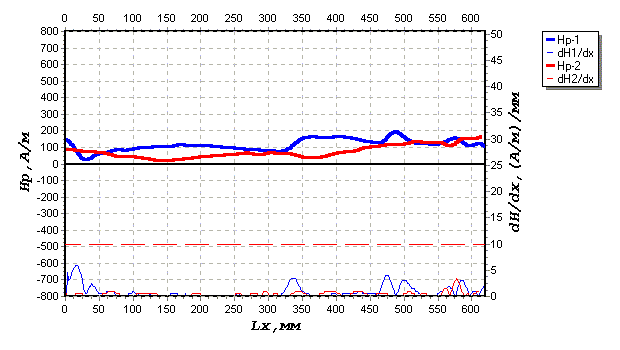
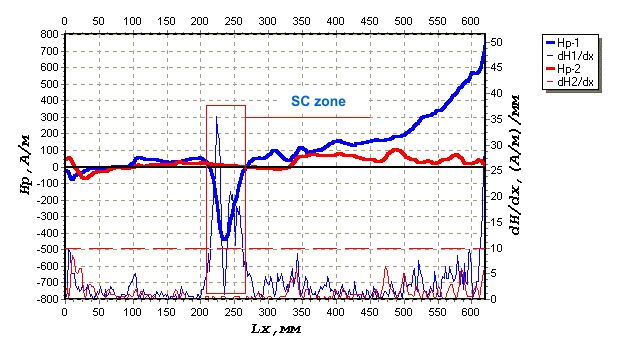
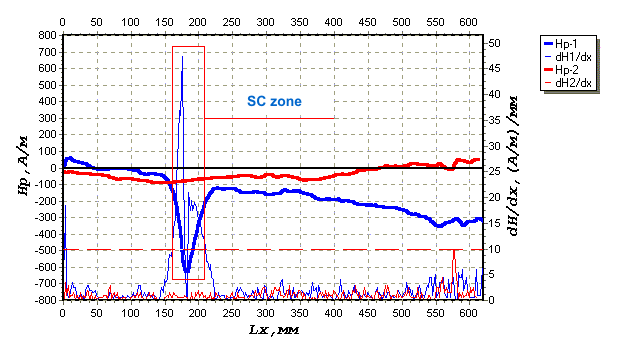
Fig.3 shows the stress concentration zones with maximal value of the field gradient dH/dx (Kin). Stress concentration zones are detected in the sites of sign alternation of Hp field. Shown Hp=0 lines are detected during the more datailed inspection of the blades #32 and #33. In these stress concentration zones development of the blades damaging should be expected. It is was verified by the metallographic investigation.
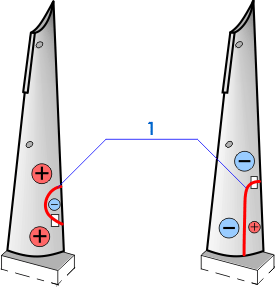
The pronounced corrosion-fatigue damaging of the metal, corresponding to the pre-failure state of the blades #32 and #33, can be seen on the structure fragments (magnification ×500) shown in fig.4,a and 4,b.
It should be noted that the maximum damaging of the metal's structure was detected in the course of investigations exactly in the zones of the maximum Hp field gradient recorded during the inspection near the SC line. The metal's structure is satisfactory at a distance of just 100 micrometers from the SC line (for example, see the structure fragment shown in fig.4, c for the blade #33).
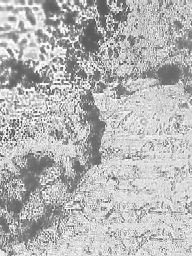
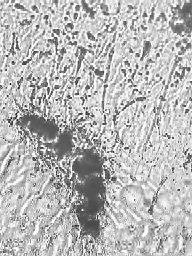
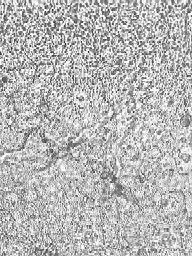
Of the total number of more than 800 LPR blades, inspected using the metal magnetic memory method, only three blades in the pre-failure state were detected. The non-failure operating time of these blades was ~ 200000 hours at the date of inspection.
In the course of the industrial verification of the considered inspection method Energodiagnostika Co. Ltd. accumulated the data bank of the numerical Kin values for the blades in the pre-failure state for the last stages of the PT-60-130, K-100, K-200 and K-300 turbines.